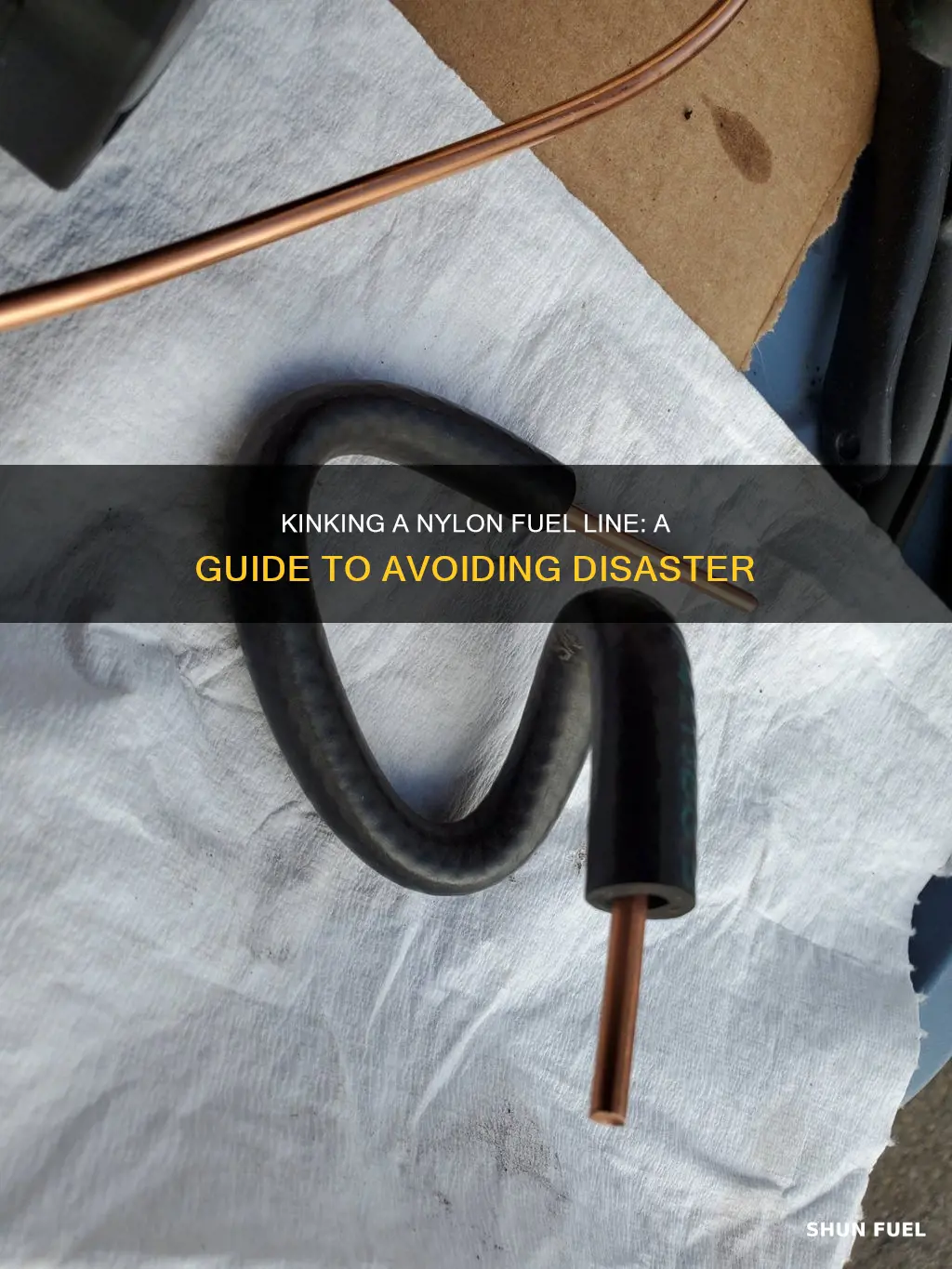
Installing a nylon fuel line can be a tricky task, and one common issue that arises is kinking the line. Kinking occurs when the fuel line is bent or twisted, creating a sharp bend or kink. This can lead to several problems, including reduced fuel flow, potential fuel leaks, and even damage to the fuel line itself. Understanding the causes and consequences of kinking is crucial for any installer to ensure a successful and safe installation. In this discussion, we will explore the various aspects of kinking a nylon fuel line and provide insights into how to avoid and mitigate this issue during the installation process.
What You'll Learn
- Safety Hazards: Kinking nylon fuel lines can cause fuel leaks, leading to potential fires and explosions
- Performance Issues: Kinking can restrict fuel flow, reducing engine performance and potentially causing stalling
- Durability Concerns: Kinking may damage the fuel line, reducing its lifespan and requiring premature replacement
- Maintenance Challenges: Kinking can make it difficult to access and maintain the fuel system
- Legal and Insurance Implications: Kinking may void warranties and insurance coverage, leading to costly repairs
Safety Hazards: Kinking nylon fuel lines can cause fuel leaks, leading to potential fires and explosions
Kinking a nylon fuel line during installation is a critical issue that can have severe safety implications. Nylon fuel lines are commonly used in automotive applications due to their flexibility and durability, but they are also susceptible to kinking, especially when bent or twisted sharply. This kinking can lead to several hazardous consequences, primarily related to fuel leaks and the potential for fires and explosions.
When a nylon fuel line is kinked, it creates a sharp bend or crease in the material. This deformation can cause the fuel line to constrict, reducing the flow of fuel or completely blocking the passage. As a result, the fuel may not reach the engine efficiently, leading to poor performance or even engine failure. However, the more significant concern is the potential for fuel leaks. The kinked section of the fuel line can develop small cracks or tears, allowing fuel to escape. This is particularly dangerous as fuel is highly flammable, and any leak can quickly escalate into a fire hazard.
The risk of fire and explosion becomes even more apparent when considering the proximity of fuel lines to various engine components and hot surfaces. Engine compartments are often warm or hot, and the presence of a fuel leak can lead to rapid ignition of the spilled fuel. This can result in a small fire that may quickly spread, causing significant damage to the vehicle and posing a serious risk to the driver and passengers. In extreme cases, a fire caused by a fuel leak could lead to an explosion, especially if the fuel vapor ignites in a confined space.
To mitigate these hazards, it is crucial to handle nylon fuel lines with care during installation. Avoid sharp bends and twists, and ensure that the lines are routed in a way that minimizes the risk of kinking. Using appropriate tools and following manufacturer guidelines can help prevent kinking and ensure a secure, leak-free connection. Additionally, regular inspections of fuel lines, especially those in high-stress areas, can help identify and address any potential issues before they lead to dangerous situations.
In summary, kinking a nylon fuel line while installing can have severe safety consequences. It can cause fuel leaks, which in turn increase the risk of fires and explosions. Proper installation techniques and regular maintenance are essential to prevent these hazards and ensure the safe operation of vehicles.
Fitting Fuel: Compatibility of 3/16 Fuel Lines with 1/4 Filters
You may want to see also
Performance Issues: Kinking can restrict fuel flow, reducing engine performance and potentially causing stalling
Kinking a nylon fuel line during installation can have significant performance implications for your engine. When a fuel line is kinked, it creates a restriction in the flow of fuel, which can lead to a multitude of issues that directly impact the engine's performance. The primary concern is the reduced fuel flow, which can cause the engine to run inefficiently or even stall.
The engine's performance is highly dependent on the smooth and consistent delivery of fuel. When a fuel line is kinked, it narrows the internal diameter, effectively reducing the cross-sectional area through which the fuel can flow. This restriction limits the volume of fuel that can pass through the line per unit of time, resulting in a reduced fuel supply to the engine. As a consequence, the engine may not receive the necessary amount of fuel to maintain optimal combustion, leading to a decrease in power output and overall performance.
In more severe cases, the reduced fuel flow can cause the engine to stall. When the fuel supply is insufficient, the engine may not have enough power to maintain stable operation, causing it to shut down. This is particularly problematic during critical moments, such as taking off or climbing at high altitudes, where maintaining engine power is crucial. Stalling can also occur when the engine is under load, as the reduced fuel flow may not be sufficient to meet the increased demand for power.
To ensure optimal engine performance, it is essential to install fuel lines correctly and avoid any kinking or bending that could restrict fuel flow. Proper installation techniques, such as using flexible fuel lines and ensuring they are not tightly bent or twisted, can help prevent performance issues. Regular inspections and maintenance of the fuel system can also identify and rectify any potential issues, ensuring that the engine operates efficiently and reliably.
In summary, kinking a nylon fuel line during installation can have detrimental effects on engine performance. The restriction in fuel flow can lead to reduced power output, inefficient combustion, and, in extreme cases, engine stalling. Proper installation techniques and regular maintenance are crucial to prevent these performance issues and ensure the longevity and reliability of the engine.
Mastering the Art of Soldering Fuel Lines: A Comprehensive Guide
You may want to see also
Durability Concerns: Kinking may damage the fuel line, reducing its lifespan and requiring premature replacement
Kinking a nylon fuel line during installation can have significant durability concerns and may lead to premature replacement. The process of kinking involves bending or twisting the fuel line to create a sharp bend, which can cause several issues. Firstly, the kinked section becomes more susceptible to damage from external factors. Nylon fuel lines are designed to be flexible and durable, but the kinked area can become a weak point, especially when subjected to vibrations, temperature changes, or pressure fluctuations during vehicle operation. Over time, this weakness can lead to cracks, splits, or even complete rupture of the fuel line.
The impact of kinking is twofold. Initially, it may cause immediate damage to the fuel line's structure, leading to reduced flow capacity or even complete blockage. This can result in fuel starvation to the engine, causing it to stall or perform poorly. Moreover, the kinked line can create a source of stress and potential failure points, especially at the kinked area. As the vehicle ages and undergoes various driving conditions, the kinked line may continue to deteriorate, leading to more frequent and severe issues.
In the long term, kinking can significantly reduce the overall lifespan of the fuel line. The repeated bending and stress on the kinked section can accelerate wear and tear, causing the nylon material to degrade faster. This degradation can result in a loss of flexibility, making the fuel line more prone to cracking or splitting under pressure. As a consequence, fuel leaks may occur, posing a safety hazard and potentially causing engine misfires or complete failure.
To avoid these durability concerns, it is crucial to follow proper installation techniques and guidelines. Fuel line manufacturers often provide specific instructions on how to handle and install their products to ensure optimal performance and longevity. These instructions typically emphasize the importance of avoiding sharp bends and kinks, suggesting alternative methods such as using fuel line protectors or following a more gradual bending process. By adhering to these recommendations, vehicle owners can minimize the risk of kinking-related damage and ensure the fuel system's reliability over time.
In summary, kinking a nylon fuel line during installation can have severe consequences for the fuel system's durability. It may lead to immediate issues like reduced flow or blockage, as well as long-term problems such as accelerated wear, cracks, and potential fuel leaks. To maintain the integrity of the fuel line and ensure the engine's performance, it is essential to install the fuel line correctly, avoiding sharp bends and following manufacturer guidelines. Regular inspections and maintenance can also help identify and address any kinking-related damage before it becomes a major problem.
Fuel Line Removal Guide: 2005 Ford Ranger
You may want to see also
Maintenance Challenges: Kinking can make it difficult to access and maintain the fuel system
Kinking a nylon fuel line during installation can present significant maintenance challenges, especially when it comes to accessing and servicing the fuel system. This issue often arises due to the line's tendency to restrict movement and flexibility, making it a complex task to reach the necessary components. When kinking occurs, the fuel line becomes rigid and prone to causing damage to other parts of the system, such as fuel injectors or pumps.
One of the primary maintenance challenges is the difficulty in identifying and reaching the affected area. Kinked lines may not be immediately noticeable, and their position can vary, making it a time-consuming process to locate the problem. This complexity is further exacerbated when the engine is in operation, as the fuel line's position changes with engine movement, making it even harder to inspect and repair.
In many cases, kinking can lead to fuel leaks, which pose a serious safety hazard. The restricted flow and potential damage to the line can cause fuel to spill, creating a fire risk. Additionally, the kinked line may not provide the necessary pressure for efficient fuel delivery, leading to poor engine performance. Maintenance personnel must carefully inspect the entire fuel system to identify any other potential issues that may have been caused by the kink.
To address these challenges, it is crucial to employ proper installation techniques and use appropriate tools to prevent kinking. Ensuring the fuel line is properly secured and flexible during installation can significantly reduce the likelihood of kinking. Regular maintenance and inspections are also essential to identify any issues early on, allowing for prompt repairs and minimizing the risk of further complications.
In summary, kinking a nylon fuel line during installation can lead to complex maintenance issues. The restricted access and potential damage to the fuel system require careful inspection and specialized tools to address. By understanding the challenges and implementing preventive measures, technicians can ensure the longevity and reliability of the fuel system, ultimately contributing to the overall performance and safety of the vehicle.
Craftsman Push Mower Fuel Line Sizes: A Comprehensive Guide
You may want to see also
Legal and Insurance Implications: Kinking may void warranties and insurance coverage, leading to costly repairs
Kinking a nylon fuel line during installation can have significant legal and financial repercussions, potentially voiding warranties and insurance coverage, and resulting in expensive repairs. This critical issue often arises from improper installation techniques, such as sharp bends or excessive tension, which can compromise the line's integrity. When a fuel line is kinked, it can lead to reduced flow, blockages, or even complete rupture, posing serious risks to the vehicle's performance and safety.
In the context of warranties, manufacturers typically provide coverage for defects in materials and workmanship. However, kinking a fuel line during installation can be considered a user error or negligence, which may void these warranties. This means that any subsequent issues, such as fuel leaks or engine damage, could be the responsibility of the installer, leading to costly repairs at their expense. It is essential for installers to adhere to manufacturer guidelines and best practices to ensure that the fuel lines are installed correctly and safely.
Insurance coverage can also be affected by kinking a fuel line. Standard auto insurance policies generally cover damage caused by accidents or natural disasters but may exclude coverage for issues resulting from improper installation. If a kinked fuel line leads to a fuel leak or engine failure, the insurance company might deny the claim, leaving the installer or vehicle owner responsible for the repairs. This can be particularly challenging if the installation was performed by a third party, as the onus of responsibility may shift between the installer and the policyholder.
To mitigate these legal and financial risks, it is crucial to follow established installation procedures and guidelines. Installers should ensure that fuel lines are routed correctly, secured properly, and free from sharp bends or excessive stress. Using the right tools and techniques, such as fuel line cutters and crimping tools, can help prevent kinking and ensure a professional installation. Additionally, maintaining detailed records of the installation process, including photographs and written documentation, can provide evidence of proper procedure and potentially protect against warranty and insurance issues.
In summary, kinking a nylon fuel line during installation can have far-reaching consequences, including legal and financial liabilities. Installers must be vigilant in their approach, adhering to manufacturer instructions and industry standards to avoid voiding warranties and insurance coverage. By taking the necessary precautions and following best practices, installers can ensure the safety and reliability of the vehicle's fuel system while minimizing the risk of costly repairs and potential legal disputes.
Barbed Nylon Fuel Line: Compatibility and Installation Guide
You may want to see also
Frequently asked questions
Kinking a nylon fuel line can lead to several issues. Firstly, it can cause a restriction in the fuel flow, resulting in reduced engine performance or even stalling. The kinked line may also lead to fuel accumulation in the line, which can cause pressure build-up and potential fuel line damage over time. Additionally, kinks can lead to fuel leaks, posing a fire hazard and environmental risk.
To prevent kinking, it is essential to plan the installation route carefully. Keep the fuel line as straight as possible and avoid sharp bends or tight turns. Use appropriate support or guides to maintain the line's shape and ensure it doesn't come into contact with sharp edges or protruding objects. Properly secure the line to prevent any accidental movement or kinking.
Yes, there are a few techniques to minimize kinking. One method is to use a fuel line protector or a flexible hose guide to support the line and maintain its shape. You can also consider using a fuel line with a built-in flexible core, which provides some give and reduces the likelihood of kinking. Additionally, taking regular breaks during installation to inspect and adjust the line can help identify and rectify any potential kinks early on.