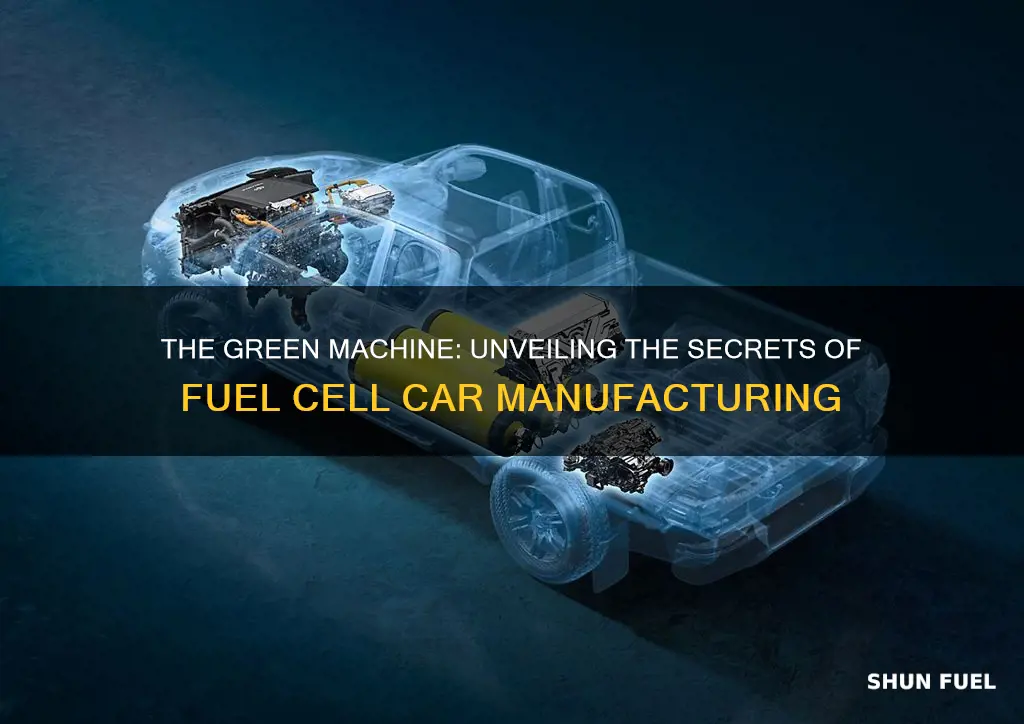
Fuel cell cars are a promising alternative to traditional internal combustion engine vehicles, and their production process involves several intricate steps. The manufacturing of these vehicles begins with the creation of a fuel cell stack, which is the heart of the car's power system. This stack is composed of multiple layers of fuel cell membranes, catalysts, and bipolar plates, all meticulously assembled to facilitate the electrochemical reaction between hydrogen and oxygen, producing electricity. The process also includes the integration of a storage system for hydrogen fuel, an electric motor, and a control unit to manage the entire power train. The manufacturing process demands precision and advanced engineering to ensure the efficiency and reliability of these vehicles, contributing to a greener and more sustainable transportation future.
What You'll Learn
- Design and Manufacturing: Prototyping, engineering, and mass production techniques
- Fuel Cell Assembly: Stacking fuel cells, bipolar plates, and gaskets
- Power Electronics: Converters, inverters, and DC-DC converters for efficient energy transfer
- Storage and Distribution: Hydrogen tanks, fuel lines, and fuel cell cooling systems
- Safety and Regulation: Emission control, pressure management, and safety protocols
Design and Manufacturing: Prototyping, engineering, and mass production techniques
The process of designing and manufacturing a fuel cell car involves intricate engineering and innovative manufacturing techniques. Prototyping is a crucial initial phase, where engineers create scale models and mock-ups to test and refine the vehicle's design. These prototypes are built using advanced 3D printing technology, allowing for rapid iteration and the ability to test various components and systems. The prototypes are then rigorously tested in wind tunnels and on test tracks to evaluate aerodynamics, handling, and overall performance.
Engineering plays a pivotal role in the development of fuel cell cars. Engineers focus on optimizing the vehicle's power-to-weight ratio, ensuring efficient energy conversion and storage. They design the fuel cell stack, which is the heart of the car, consisting of multiple fuel cells arranged in a stack. Each fuel cell generates electricity through an electrochemical reaction between hydrogen and oxygen, producing electricity, water, and heat. Engineers also work on the vehicle's electrical and mechanical systems, integrating the fuel cell stack with the drivetrain and other essential components.
Mass production techniques for fuel cell cars present unique challenges. The manufacturing process requires precision and specialized equipment. Assembly lines are designed to handle the delicate nature of fuel cell components, ensuring proper alignment and sealing. Robotic arms and automated systems are employed to position and secure the fuel cell stack, batteries, and other modules. Advanced welding techniques are utilized to join the vehicle's body and chassis, maintaining structural integrity. Quality control is paramount, with rigorous testing and inspection at each production stage to ensure the reliability and safety of the fuel cell car.
The manufacturing process also involves the production of hydrogen storage tanks and fuel delivery systems. These components require specialized welding and sealing techniques to ensure the safe and efficient storage and supply of hydrogen gas. Advanced materials, such as carbon fiber composites, are often used to reduce weight and improve structural performance. The manufacturing process also includes the integration of various electronic control units (ECUs) and sensors to monitor and control the fuel cell system's performance.
In summary, the design and manufacturing of fuel cell cars involve a complex interplay of prototyping, engineering, and mass production techniques. Prototyping enables the refinement of the vehicle's design, while engineering focuses on optimizing power and efficiency. Mass production requires specialized equipment and processes to handle the unique components of fuel cell cars, ensuring their reliability and safety. The result is a cutting-edge vehicle that offers a sustainable and efficient mode of transportation.
Gender and Fuel Efficiency: Who's Behind the Wheel?
You may want to see also
Fuel Cell Assembly: Stacking fuel cells, bipolar plates, and gaskets
The assembly of a fuel cell stack is a crucial step in the manufacturing process of a fuel cell vehicle, and it involves precise engineering to ensure optimal performance and efficiency. This process begins with the stacking of individual fuel cells, which are the core components of the fuel cell system. Each fuel cell consists of an anode and cathode catalyst layer, a polymer electrolyte membrane, and a pair of gas diffusion layers (GDLs). These cells are then carefully arranged to form a stack, which is the heart of the fuel cell system.
When stacking the fuel cells, the bipolar plates play a vital role. These plates are designed with a central flow field that allows for the distribution of reactant gases (typically hydrogen and oxygen) to the anode and cathode, respectively. The bipolar plates are positioned between the fuel cells, with the anode gas flow channel on one side and the cathode gas flow channel on the other. This arrangement facilitates the efficient transport of reactants to the catalyst layers while also providing a path for the removal of reaction products.
Gaskets are an essential component of the fuel cell stack assembly. They are positioned between the fuel cells and the bipolar plates to ensure a tight seal and prevent any leakage of gases. These gaskets are typically made of a durable, flexible material that can withstand the high-pressure environment within the fuel cell stack. The gaskets also help to maintain the structural integrity of the stack by providing a buffer between the cells and plates, allowing for slight variations in dimensions during the manufacturing process.
The stacking process requires precision and attention to detail. Each fuel cell must be aligned properly with its corresponding bipolar plate, ensuring that the gas flow channels are correctly oriented. The gaskets are carefully positioned to create a uniform seal around the stack, preventing any potential leaks that could compromise the system's efficiency and safety. This assembly process is often automated to ensure consistency and accuracy, with specialized equipment handling the precise placement of components.
Once the fuel cells are stacked, the entire assembly is carefully inspected to verify the integrity of the connections and seals. This includes checking for any signs of gas leakage and ensuring that the stack operates within the desired pressure and temperature ranges. The final fuel cell stack is then integrated into the vehicle's power system, where it will convert chemical energy from the fuel into electrical energy, providing the power required to propel the vehicle.
Unveiling the Fuel Injection Mystery: Do Cars Need Them?
You may want to see also
Power Electronics: Converters, inverters, and DC-DC converters for efficient energy transfer
Power electronics play a crucial role in the efficient energy transfer and management within fuel cell vehicles, which are becoming increasingly popular as a sustainable transportation alternative. These vehicles utilize fuel cells to generate electricity, which is then used to power electric motors and drive the vehicle. The efficiency of this process relies heavily on the use of power electronics components, specifically converters, inverters, and DC-DC converters.
Converters:
Converters are essential for fuel cell cars as they facilitate the conversion of the direct current (DC) output of the fuel cell into alternating current (AC) required by the electric motor. This process involves rectifying the fuel cell's DC voltage to a higher DC voltage, which is then converted to AC using an inverter. The converters ensure that the electrical energy is compatible with the vehicle's power system, allowing for efficient operation.
Inverters:
Inverters are critical components in the power electronics system of fuel cell vehicles. Their primary function is to convert the DC output from the fuel cell stack into AC power, which is suitable for driving the electric motor. Inverters must handle high power levels and provide precise control over the motor's speed and torque. Modern inverters use sophisticated control algorithms to ensure smooth acceleration and deceleration, contributing to the overall efficiency and performance of the vehicle.
DC-DC Converters:
DC-DC converters are used to regulate and adjust the voltage levels within the fuel cell system. These converters are crucial for optimizing the power distribution and ensuring that the various components receive the required voltage. In fuel cell cars, DC-DC converters are employed to step down the high voltage from the fuel cell stack to the lower voltage levels needed by other subsystems, such as the battery, charger, and auxiliary equipment. This efficient voltage regulation helps in minimizing energy losses and improving overall system efficiency.
The integration of these power electronics components allows fuel cell cars to efficiently convert and manage the energy generated by the fuel cells. By utilizing converters, inverters, and DC-DC converters, the vehicles can ensure that the electrical energy is compatible, controlled, and distributed optimally throughout the system. This efficient energy transfer is a key factor in the successful operation and performance of fuel cell vehicles, making them a promising solution for sustainable transportation.
Flex Fuel: Friend or Foe? Uncovering the Truth
You may want to see also
Storage and Distribution: Hydrogen tanks, fuel lines, and fuel cell cooling systems
The storage and distribution of hydrogen in fuel cell vehicles is a critical aspect of their design and functionality. Hydrogen fuel cell cars require specialized storage systems to safely and efficiently store the hydrogen gas used as fuel. These systems are designed to meet the unique challenges posed by hydrogen's properties, including its low density and high reactivity.
Hydrogen tanks are a key component of this storage system. These tanks are typically made of composite materials, such as carbon fiber-reinforced polymers, which offer a balance of strength and lightweight design. The tanks are engineered to withstand high pressures, often exceeding 5,000 pounds per square inch (psi), to ensure the safe containment of hydrogen. The design and placement of these tanks are crucial to optimize space utilization within the vehicle's structure while maintaining structural integrity.
Fuel lines play a vital role in the distribution of hydrogen from the storage tanks to the fuel cells. These lines are made of specialized materials, such as high-strength, flexible polymers, capable of withstanding the corrosive effects of hydrogen and the high pressures involved. The fuel lines are carefully routed through the vehicle, often following a path that minimizes the risk of damage and ensures efficient delivery of hydrogen to the fuel cells.
In addition to storage and distribution, cooling systems are essential for maintaining the optimal operating temperature of the fuel cells. Hydrogen fuel cells operate most efficiently within a specific temperature range. Therefore, cooling systems are employed to prevent overheating and ensure consistent performance. These cooling systems can utilize various methods, such as liquid cooling or air cooling, depending on the vehicle's design and requirements. The cooling system is designed to dissipate heat generated during the electrochemical reactions, ensuring the fuel cell operates within safe temperature limits.
The integration of these storage, distribution, and cooling systems is a complex process that requires careful engineering and design. It involves optimizing the placement of hydrogen tanks, fuel lines, and cooling components to ensure efficient and safe operation. This intricate design process ensures that fuel cell vehicles can store and utilize hydrogen effectively while maintaining the overall structural integrity and performance of the vehicle.
Electric Cars: Do They Burn Fossil Fuels?
You may want to see also
Safety and Regulation: Emission control, pressure management, and safety protocols
The integration of fuel cell technology in automobiles presents unique challenges and opportunities, particularly in terms of safety and regulation. Fuel cell vehicles (FCVs) operate on a different power source compared to conventional internal combustion engines, and their design and operation require careful consideration of emission control, pressure management, and stringent safety protocols.
Emission Control:
One of the most significant advantages of fuel cell cars is their potential to produce zero tailpipe emissions. This is achieved through the electrochemical reaction of hydrogen and oxygen, resulting in the production of electricity and water as the only byproducts. However, ensuring that no harmful emissions are released during the refueling process is crucial. Refueling stations must be designed to prevent the release of hydrogen gas, which is highly flammable, and to capture any potential leaks. Advanced monitoring systems are employed to detect and mitigate any emissions, ensuring compliance with environmental regulations.
Pressure Management:
Fuel cell vehicles operate under high-pressure conditions, typically ranging from 350 to 700 bars (5,000 to 10,000 psi). This high pressure is necessary to store and supply hydrogen efficiently. To ensure safety, the fuel cell system incorporates pressure-regulating mechanisms. These include pressure-relief valves, pressure sensors, and sophisticated control systems that monitor and adjust pressure levels. In the event of a pressure surge or leak, these systems are designed to respond rapidly, releasing the excess pressure or initiating emergency protocols to prevent potential hazards.
Safety Protocols:
Safety is a paramount concern in fuel cell car manufacturing and operation. The vehicles are equipped with advanced safety features to protect both the occupants and the surrounding environment. Here are some key safety measures:
- Hydrogen Leak Detection: Fuel cell cars employ sensitive sensors to detect even minute traces of hydrogen leaks. These sensors can identify leaks in the fuel tank, fuel lines, and fuel cell stack, triggering alerts and initiating emergency procedures.
- Fire Safety: Despite the low risk of fire due to the absence of flammable liquids, fire safety measures are still essential. These include fire suppression systems, such as inert gas blankets or fire extinguishers, designed to respond to potential fire hazards.
- Emergency Shutdown: In the event of a malfunction or accident, the vehicle's control system can initiate an emergency shutdown. This process involves cutting off power to the fuel cell, isolating the hydrogen supply, and implementing safety protocols to prevent further risks.
- Regulation Compliance: Fuel cell vehicle manufacturers must adhere to strict regulations and standards set by governing bodies. These regulations cover various aspects, including vehicle design, construction, testing, and operation, ensuring that FCVs meet safety and environmental criteria.
The development of fuel cell cars involves a comprehensive approach to safety and regulation, addressing the unique challenges posed by hydrogen-based energy systems. Through advanced emission control, precise pressure management, and robust safety protocols, these vehicles can operate efficiently while minimizing risks to both human and environmental health.
Flex Fuel Cars: Maintenance Tips for Easy Ownership
You may want to see also
Frequently asked questions
Fuel cell vehicles are typically constructed using lightweight materials such as carbon fiber composites, aluminum alloys, and advanced steel alloys. These materials are chosen for their strength-to-weight ratio, allowing for efficient energy storage and transmission while reducing the overall weight of the vehicle.
The fuel cell stack is the heart of the fuel cell car. It consists of multiple fuel cell modules, each containing an anode, cathode, and electrolyte. These modules are carefully stacked and secured together, with each module connected to the next via gaskets and seals. The stack is then integrated into the vehicle's chassis, ensuring proper cooling and ventilation.
Integrating the fuel cell system requires careful engineering to fit the components within the car's structure. This includes designing the fuel tank, fuel supply lines, and the placement of the fuel cell stack, often in the vehicle's underbody or rear compartment. The goal is to optimize space utilization while ensuring easy access for maintenance and refueling.
Fuel cell cars often feature a combination of fuel cell power and battery storage systems. The electrical components, including inverters, converters, and control units, are carefully managed to ensure efficient power distribution. The batteries store excess energy and provide additional power when needed, especially during acceleration or when the fuel cell is temporarily inactive.
Manufacturing a fuel cell car involves several critical steps: chassis assembly, fuel cell stack integration, electrical system installation, and comprehensive testing. Each component is meticulously engineered and assembled, followed by rigorous quality control checks. The final assembly process ensures that all systems work harmoniously, and the vehicle meets safety and performance standards.