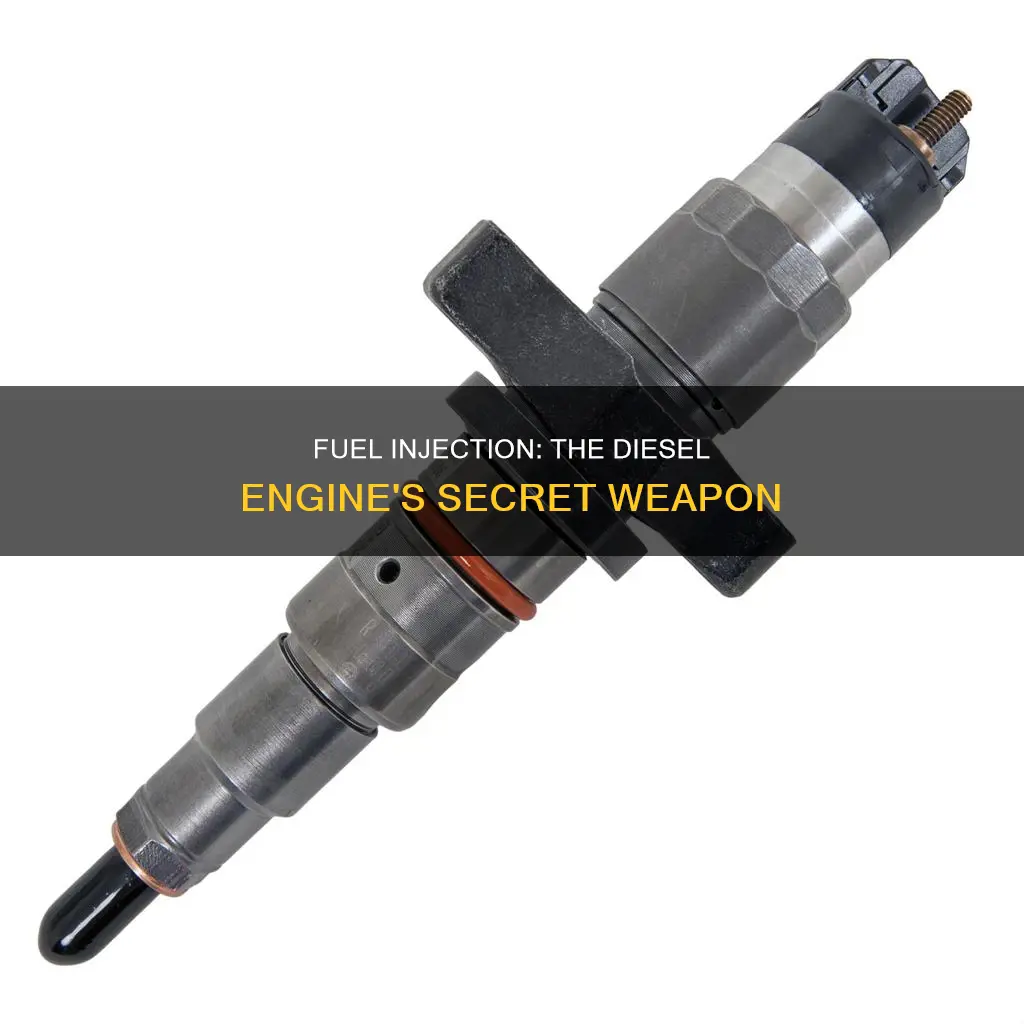
Diesel cars, known for their robust engines and fuel efficiency, rely on a different fueling system compared to gasoline vehicles. One of the key components in these engines is the fuel injector, which plays a crucial role in delivering fuel to the engine's combustion chamber. Unlike gasoline cars, diesel engines use a process called direct injection, where fuel is injected directly into the combustion chamber at high pressure. This process is facilitated by the fuel injectors, which precisely control the amount of fuel entering the engine, ensuring optimal performance and efficiency. Understanding the role of fuel injectors in diesel cars is essential for anyone interested in the mechanics of these vehicles.
What You'll Learn
- Fuel Injection Systems: Diesel engines use injectors to precisely deliver fuel into the combustion chamber
- Injection Timing: Timing of fuel injection is crucial for optimal performance and emissions
- Fuel Pressure Regulation: Injectors operate under high pressure to ensure efficient fuel atomization
- Common Rail Systems: Many modern diesels use common rail injectors for improved power and efficiency
- Fuel Efficiency: Efficient fuel injection contributes to better fuel economy in diesel vehicles
Fuel Injection Systems: Diesel engines use injectors to precisely deliver fuel into the combustion chamber
The fuel injection system in diesel engines is a crucial component that ensures efficient and powerful performance. Unlike gasoline engines, diesel engines rely on a different approach to fuel delivery, and this is where fuel injectors come into play. These injectors are responsible for precisely injecting fuel into the combustion chamber, a process that is both complex and highly engineered.
In a diesel engine, fuel is injected directly into the combustion chamber, which is a significant departure from the carburetor-based systems found in older gasoline engines. The fuel injectors in diesel engines are designed to deliver fuel at high pressure, ensuring that it atomizes and mixes thoroughly with the air-fuel mixture. This high-pressure injection process is a key factor in the efficiency and power output of diesel engines.
The operation of fuel injectors in diesel engines is a precise and timed process. When the engine's computer system determines the optimal amount of fuel required for a specific cylinder and engine speed, it sends an electric signal to the injector. This signal triggers the injector to open and release the fuel at the precise moment, ensuring that it is injected into the combustion chamber when the engine's piston is at the correct position. This timing is critical for optimal combustion and performance.
Diesel fuel injectors are typically located in the engine block, close to the combustion chamber, and are designed to handle the high pressure required for efficient fuel delivery. The injectors are often arranged in a line, with each injector responsible for a specific cylinder. This arrangement allows for precise control over the fuel injection process, ensuring that each cylinder receives the exact amount of fuel needed for optimal performance.
Modern diesel engines often feature advanced fuel injection systems that include electronic controls and precision injectors. These systems can adjust the fuel injection rate and timing based on various engine parameters, such as speed, load, and temperature. This level of control contributes to improved engine performance, reduced emissions, and enhanced overall efficiency, making diesel engines a popular choice for heavy-duty vehicles and applications where power and torque are essential.
Unlocking the Mystery: Can Regular Fuel Be Used in Premium Fuel Additives?
You may want to see also
Injection Timing: Timing of fuel injection is crucial for optimal performance and emissions
The timing of fuel injection is a critical aspect of diesel engine operation, playing a pivotal role in achieving optimal performance and minimizing emissions. In diesel engines, fuel is injected into the combustion chamber at precise moments to ensure efficient combustion and power output. This process is a far cry from the simpler carburetor systems found in gasoline engines, where the fuel-air mixture is created and controlled in a different manner.
Injection timing refers to the exact moment when the fuel is injected into the engine's cylinders. This timing is crucial because it directly impacts the air-fuel mixture's quality and the combustion process. If the fuel is injected too early, it can lead to incomplete combustion, resulting in reduced power and increased emissions of unburned hydrocarbons. Conversely, injecting fuel too late can cause excessive smoke and carbon monoxide emissions due to incomplete burning.
The timing is controlled by the engine's electronic control unit (ECU), which monitors various parameters such as engine speed, load, and temperature. Based on this data, the ECU adjusts the fuel injection timing to optimize performance and emissions. Modern diesel engines use sophisticated sensors and actuators to ensure that the fuel is injected precisely when needed. For instance, a camshaft position sensor helps the ECU determine the correct injection timing relative to the engine's piston position.
Optimizing injection timing is essential for meeting stringent environmental regulations. By ensuring that fuel is injected at the right moment, diesel engines can achieve leaner combustion, which reduces the formation of harmful pollutants like nitrogen oxides (NOx) and particulate matter. This is particularly important in heavy-duty applications, where diesel engines are commonly used, as these vehicles have a significant environmental impact.
In summary, the timing of fuel injection is a critical parameter in diesel engine design and operation. It directly influences performance, emissions, and the overall efficiency of the engine. Through precise timing control, diesel engines can deliver the power and torque expected from these vehicles while adhering to strict environmental standards.
Gas Car Fuel Filters: What You Need to Know
You may want to see also
Fuel Pressure Regulation: Injectors operate under high pressure to ensure efficient fuel atomization
The fuel injection system in diesel engines is a critical component that ensures optimal performance and efficiency. One of the key aspects of this system is fuel pressure regulation, which is where the injectors play a vital role. These injectors are designed to operate under extremely high pressure, typically ranging from 300 to 2000 bar (43,500 to 290,000 psi), depending on the engine's specifications. This high-pressure environment is necessary to achieve efficient fuel atomization, a process that is fundamental to the combustion process in diesel engines.
When the engine is running, the fuel pressure regulator ensures that the fuel pressure remains stable and within a precise range. This regulation is crucial because it directly impacts the engine's performance and emissions. If the pressure is too low, the fuel may not atomize properly, leading to incomplete combustion and reduced power output. Conversely, if the pressure is too high, it can cause excessive fuel atomization, resulting in a loss of power and potential engine damage.
The injectors are designed with precision to deliver the correct amount of fuel at the right pressure at each injection event. This is achieved through a complex mechanism that includes a high-pressure pump, a pressure regulator, and the injectors themselves. The pump increases the fuel pressure, and the regulator maintains it within a specified range, ensuring that the fuel is delivered to the injectors at the optimal pressure for efficient atomization.
Efficient fuel atomization is essential for the combustion process in diesel engines. When the fuel is atomized, it breaks down into tiny droplets, increasing the surface area and allowing for better mixing with the air-fuel mixture. This results in a more complete combustion process, which produces more power and less harmful emissions. The high pressure ensures that the fuel is injected with sufficient force to create these fine droplets, optimizing the engine's performance.
In summary, the fuel pressure regulation system in diesel engines, which relies on the high-pressure operation of fuel injectors, is a critical component for efficient fuel atomization. This process ensures that the engine operates optimally, delivering power and performance while minimizing emissions. Understanding the role of fuel injectors and their pressure requirements is essential for maintaining and optimizing diesel engine performance.
Summer Car Fueling: Tractors and Their Power Sources
You may want to see also
Common Rail Systems: Many modern diesels use common rail injectors for improved power and efficiency
The evolution of diesel engine technology has led to significant advancements in fuel injection systems, with one of the most notable innovations being the Common Rail System. This system has become a hallmark of modern diesel engines, offering a range of benefits that contribute to improved power, efficiency, and overall performance.
In the context of diesel engines, fuel injectors play a critical role in delivering fuel to the combustion chamber. Traditional diesel engines often utilized mechanical fuel injection systems, which, while effective, had limitations in terms of precision and control. Common rail systems, however, take a different approach by utilizing a high-pressure fuel rail, which acts as a reservoir for the fuel. This design innovation allows for a more precise and controlled fuel injection process.
At the heart of the Common Rail System is the high-pressure pump, which generates and maintains a high-pressure fuel rail. This pump ensures that the fuel is delivered at the precise moment and in the correct quantity required for optimal combustion. The high pressure in the rail enables the injectors to atomize the fuel into a fine mist, which improves combustion efficiency and reduces emissions. This level of control over the fuel injection process is a significant advancement over older mechanical systems.
One of the key advantages of the Common Rail System is its ability to provide improved power output. By delivering fuel at the exact moment of combustion, the system ensures that the engine operates at its peak efficiency. This results in increased horsepower and torque, making modern diesel engines more powerful than ever before. Additionally, the precise control over fuel injection contributes to better throttle response, making the vehicle more responsive to driver input.
In terms of efficiency, the Common Rail System plays a vital role in optimizing fuel consumption. The high-pressure fuel rail allows for more accurate fuel metering, ensuring that the engine receives the right amount of fuel at all times. This precision in fuel delivery leads to improved fuel economy, which is a significant benefit for diesel vehicles, known for their excellent mileage. Furthermore, the system's ability to fine-tune combustion parameters contributes to reduced emissions, making diesel engines more environmentally friendly.
In summary, the Common Rail System is a game-changer in diesel engine technology, offering a sophisticated solution for fuel injection. Its implementation in modern diesel cars has led to a significant leap in performance, delivering improved power and efficiency. This system's ability to maintain high pressure and provide precise fuel injection control has revolutionized diesel engines, making them a preferred choice for those seeking both power and economy.
Race Fuel: Unleash the Power in Your Car?
You may want to see also
Fuel Efficiency: Efficient fuel injection contributes to better fuel economy in diesel vehicles
The concept of fuel injection is a crucial aspect of modern diesel engine technology, and it plays a significant role in enhancing fuel efficiency. Efficient fuel injection systems are designed to optimize the combustion process, ensuring that diesel engines operate with remarkable precision and performance. This technology is a far cry from the traditional carburetor systems found in gasoline engines, where the fuel and air mixture was simply drawn into the engine through a series of passages.
In diesel engines, fuel injectors are responsible for precisely metering and injecting fuel into the combustion chamber at the right time and in the correct quantity. This process is highly controlled and ensures that the fuel-air mixture is perfectly balanced, leading to more efficient combustion. The injectors spray the fuel in a fine mist, which mixes thoroughly with the air, creating a homogeneous mixture that is ideal for combustion. This level of control over the fuel injection process is a key factor in achieving better fuel economy.
The efficiency of fuel injection in diesel vehicles is evident in several ways. Firstly, it allows for a more precise control of the air-fuel ratio, which is critical for optimal combustion. Modern diesel fuel injectors can adjust the fuel flow rate and timing with incredible accuracy, ensuring that the engine always operates at the most efficient ratio. This precision results in a more complete combustion process, where more of the fuel is burned, leaving less unburned fuel in the exhaust, thus improving fuel efficiency.
Secondly, efficient fuel injection contributes to reduced emissions. By ensuring a more complete burn, diesel engines with advanced fuel injection systems produce fewer harmful pollutants, such as nitrogen oxides (NOx) and particulate matter. This not only benefits the environment but also helps diesel vehicles meet stricter emission standards and regulations.
Furthermore, the impact of efficient fuel injection on fuel economy is noticeable in terms of reduced fuel consumption. With precise fuel metering, diesel engines can deliver the required power output while using less fuel. This is particularly important for long-haul transportation and heavy-duty applications, where fuel costs can be a significant operational expense. By optimizing the fuel injection process, diesel vehicles can achieve higher mileage, making them more cost-effective and environmentally friendly.
Understanding Your Car's Fuel Efficiency: A Comprehensive Guide
You may want to see also
Frequently asked questions
Yes, all diesel engines use fuel injectors as a primary method of fuel delivery. These injectors precisely control the amount of fuel entering the engine, ensuring efficient combustion and optimal performance.
In diesel engines, fuel injectors spray a high-pressure fuel mist directly into the combustion chamber or near the intake valves. This process is known as direct injection, allowing for better control over the fuel-air mixture and improved combustion efficiency compared to older carburetor-based systems.
Yes, diesel fuel injectors differ from their gasoline counterparts in terms of design and operation. Diesel injectors typically have a higher pressure rating and are designed to handle the unique properties of diesel fuel, which has a higher viscosity and requires more precise injection timing for efficient combustion.
Upgrading or modifying fuel injectors in diesel cars is possible, but it requires careful consideration. High-performance injectors with increased flow rates can be installed to enhance power and performance, but it's crucial to ensure compatibility with the engine's other components and to follow manufacturer guidelines to avoid potential issues.