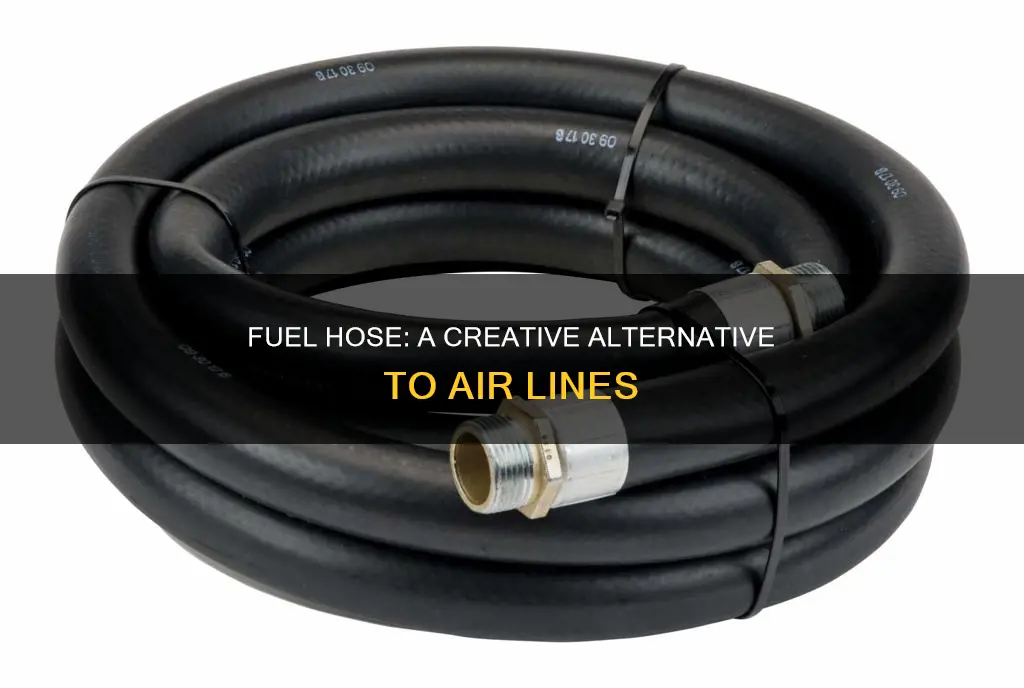
A fuel hose can be a viable alternative to an air line in certain applications. While air lines are commonly used for their ability to transmit compressed air efficiently, fuel hoses offer a cost-effective and readily available solution for specific tasks. These hoses are designed to handle fuel and can be a practical choice when an air line is not readily available or when a more flexible and adaptable option is required. This introduction sets the stage for exploring the potential uses and considerations of using fuel hoses as a replacement for air lines.
Characteristics | Values |
---|---|
Material | Fuel hoses are typically made of rubber, PVC, or synthetic materials like polyurethane, which are flexible and resistant to fuel degradation. |
Pressure Rating | They are designed to handle the pressure of fuel systems, often with higher pressure ratings compared to air lines. |
Temperature Range | Fuel hoses can withstand a wide range of temperatures, making them suitable for various climates and engine operating conditions. |
Flexibility | The hoses are flexible, allowing for easy routing and installation, especially in tight spaces. |
Chemical Resistance | They are resistant to the chemicals in fuel, ensuring longevity and preventing degradation over time. |
Cost | Fuel hoses can be more expensive than air lines, but their durability and performance make them a reliable replacement. |
Availability | These hoses are widely available and can be sourced from automotive suppliers. |
Installation | Installation may require specialized tools and knowledge due to the fuel system's complexity. |
Maintenance | Regular maintenance, such as checking for cracks or leaks, is essential to ensure the hose's longevity. |
Safety | Using the correct fuel hose can improve safety by preventing fuel leaks and potential fires. |
What You'll Learn
- Fuel Hose Material: Consider the material of the fuel hose, ensuring it's compatible with the fuel type and temperature range
- Hose Diameter: Choose a hose diameter that matches the air line's flow rate for optimal performance
- Hose Length: Determine the required length of the fuel hose, considering the distance between fuel sources and air lines
- Hose Flexibility: Ensure the hose is flexible enough to navigate through tight spaces and bends without kinking
- Hose Pressure Rating: Verify the hose's pressure rating to handle the fuel pressure and prevent leaks
Fuel Hose Material: Consider the material of the fuel hose, ensuring it's compatible with the fuel type and temperature range
When considering the use of fuel hoses as a replacement for air lines, the material of the hose is a critical factor to ensure safety and efficiency. The compatibility of the hose material with the fuel type and temperature range is essential to prevent any potential issues. Different fuels have varying chemical compositions and properties, and the hose must be able to withstand these characteristics without degradation or failure. For instance, gasoline and diesel have different boiling points and volatility levels, which can affect the hose's performance and longevity.
The temperature range is another crucial aspect. Fuel hoses need to be able to handle the extreme temperatures that can occur during fuel storage and transfer. Some fuels can become extremely hot during combustion, while others may freeze at low temperatures. Therefore, the hose material should be chosen to maintain its flexibility and integrity across this wide temperature range. Common materials used for fuel hoses include rubber, vinyl, and various synthetic compounds, each with its own advantages and limitations.
Rubber hoses are known for their flexibility and resistance to abrasion, making them suitable for many fuel types. However, they may not be ideal for high-temperature applications. Vinyl hoses, on the other hand, offer good chemical resistance and are often used for gasoline-related applications. Synthetic compounds, such as fluoropolymers, provide excellent temperature stability and chemical resistance, making them a popular choice for high-performance fuel systems.
It is essential to consult the manufacturer's guidelines and specifications when selecting the hose material. These guidelines will provide information on the recommended fuel types, temperature ranges, and pressure ratings for each hose material. Ensuring that the hose is compatible with the specific fuel and operating conditions will help prevent fuel leaks, hose failure, and potential safety hazards.
In summary, when using fuel hoses as a replacement for air lines, the material selection is a critical decision. It should be based on a thorough understanding of the fuel type, temperature range, and the specific requirements of the application. By choosing the right material, you can ensure the safety, efficiency, and longevity of the fuel hose system.
Replacing the Fuel Tank on a 2003 Kawasaki Z1000: Step-by-Step Guide
You may want to see also
Hose Diameter: Choose a hose diameter that matches the air line's flow rate for optimal performance
When considering the use of a fuel hose as a replacement for an air line, it is crucial to pay close attention to the hose's diameter. The diameter of the hose directly influences the flow rate of the air or gas it carries. Choosing the right hose diameter is essential to ensure optimal performance and prevent potential issues.
The flow rate of an air line or fuel hose determines how much air or gas can pass through it in a given time. A larger diameter hose can accommodate a higher volume of air or gas, allowing for increased flow rates. This is particularly important in applications where high-pressure air or gas is required, such as in industrial machinery or automotive systems. By selecting a hose with an appropriate diameter, you can ensure that the system can handle the required airflow or gas flow without restrictions or performance degradation.
To determine the suitable hose diameter, you need to consider the specific requirements of your application. Start by evaluating the desired flow rate of the air line or fuel hose. This can be done by consulting the manufacturer's specifications or guidelines for the particular system you are working with. Different applications may have varying flow rate needs, and it is essential to match the hose diameter accordingly. For example, if you are replacing an air line in a high-pressure pneumatic system, you might require a larger diameter hose to handle the increased flow rate and pressure.
Additionally, it is important to consider the material and construction of the hose. Some hoses are designed with specific flow rates in mind, ensuring optimal performance and compatibility with the intended use. For instance, fuel hoses are often made with materials that can withstand high-pressure fuel flow, and their diameters are chosen to match the flow rates typically encountered in fuel systems. By selecting a hose with the right material and construction, you can ensure longevity and reliable performance.
In summary, when using a fuel hose as a replacement for an air line, the hose diameter should be carefully chosen to match the flow rate requirements of the specific application. This ensures optimal performance, prevents restrictions, and guarantees the system's ability to handle the necessary airflow or gas flow. By considering the flow rate specifications and the material properties of the hose, you can make an informed decision and select the most suitable hose diameter for your needs.
Replacing Fuel Injectors in Toyota Celica: Step-by-Step Guide
You may want to see also
Hose Length: Determine the required length of the fuel hose, considering the distance between fuel sources and air lines
When considering the use of a fuel hose as a replacement for an air line, one crucial aspect to evaluate is the hose length. The required length of the fuel hose is directly related to the distance between the fuel source and the air line it needs to connect. This is an essential factor to ensure the hose can effectively deliver fuel without any issues.
To determine the appropriate hose length, start by measuring the distance between the fuel source, such as a fuel tank or a fuel pump, and the point where the air line is typically connected. This distance will vary depending on the specific vehicle or equipment setup. For example, in an automotive application, you might need to measure from the fuel tank to the engine's fuel injection system or the location of the air line connection. In industrial settings, the distance could be between a fuel supply unit and a remote air tool or compressor.
The hose length should be sufficient to accommodate this distance while also allowing for some flexibility and movement. It is important to consider that hoses can expand slightly under pressure, so a slightly longer hose might be necessary to account for any potential movement or vibration during operation. Additionally, leaving some extra length can provide easier installation and maintenance, ensuring the hose can be routed around obstacles or through tight spaces without being too tight or restrictive.
When selecting the hose, it is advisable to choose a length that is slightly longer than the measured distance. This extra length provides a safety margin and allows for better hose management. It is also important to consider the hose's bending radius and any potential restrictions in the routing path to ensure the hose can be installed and operated without damage.
In summary, determining the required hose length involves measuring the distance between the fuel source and the air line connection point, adding a small margin for flexibility, and considering the hose's characteristics. This approach ensures that the fuel hose can effectively replace the air line while providing a reliable and safe connection for fuel delivery.
Replacing Fuel Pump in 2008 Nissan Frontier: Step-by-Step Guide
You may want to see also
Hose Flexibility: Ensure the hose is flexible enough to navigate through tight spaces and bends without kinking
When considering the use of fuel hoses as a replacement for air lines, one crucial aspect to focus on is the hose's flexibility. This characteristic is essential to ensure that the hose can navigate through tight spaces and bends without any issues, such as kinking or bending out of shape.
Hoses designed for fuel transfer typically have a flexible construction, often made from materials like rubber or PVC, which allow them to bend and twist easily. This flexibility is a direct result of the hose's design, where the inner tube is surrounded by a layer of reinforcement and an outer casing. The reinforcement provides structural integrity, preventing the hose from collapsing under pressure or stress, while the outer casing offers protection against abrasion and environmental factors.
In tight spaces, such as engine compartments or behind panels, the hose's flexibility becomes even more critical. It needs to conform to the available space without putting excessive strain on the connections or causing damage to the surrounding components. A flexible hose can easily navigate these areas, ensuring a secure and reliable connection without the risk of kinking, which could lead to reduced performance or even a complete failure.
To ensure optimal flexibility, it is recommended to choose hoses with a suitable durometer, which is a measure of the material's hardness. A hose with a higher durometer will be more flexible and easier to bend, making it ideal for tight spaces. Additionally, consider the hose's length and diameter; longer hoses may require more flexibility to avoid excessive bending, and a larger diameter can provide better flexibility without compromising on strength.
In summary, when using fuel hoses as an alternative to air lines, the hose's flexibility is a key factor in ensuring a successful and reliable setup. By selecting hoses with the right material properties and dimensions, you can guarantee that the hose will navigate through tight spaces effortlessly, maintaining its integrity and performance over time.
Replacing Ryobi Trimmer Fuel Lines: A Step-by-Step Guide
You may want to see also
Hose Pressure Rating: Verify the hose's pressure rating to handle the fuel pressure and prevent leaks
When considering the use of fuel hoses as a replacement for air lines, it is crucial to prioritize safety and performance. One critical aspect to evaluate is the hose pressure rating, which directly impacts the system's reliability and efficiency. The pressure rating of a hose refers to the maximum pressure it can withstand without compromising its structural integrity. In the context of fuel systems, this rating is essential to ensure that the hose can handle the fuel pressure without leaking or failing.
Fuel systems often operate under high-pressure conditions, especially in automotive or aviation applications. Therefore, it is imperative to select hoses with an appropriate pressure rating that matches or exceeds the fuel system's requirements. A hose with a lower pressure rating may not be able to withstand the fuel pressure, leading to potential leaks, reduced performance, or even system failure.
To verify the hose pressure rating, it is recommended to consult the manufacturer's specifications and guidelines. Each hose model will have a designated pressure rating, typically indicated in units of measurement such as pounds per square inch (psi) or bar. Ensure that the chosen hose meets or exceeds the minimum pressure rating required for the specific fuel system it will be used in. This information can usually be found in the hose's technical data sheet or product documentation.
Additionally, it is essential to consider the dynamic pressure, which accounts for factors like pulsations and surges in the fuel flow. The dynamic pressure rating ensures that the hose can handle the varying pressure conditions during operation. By selecting hoses with appropriate dynamic pressure ratings, you can minimize the risk of leaks and ensure a consistent fuel supply.
In summary, when using fuel hoses as a replacement for air lines, verifying the hose pressure rating is a critical step. It ensures that the hose can safely and effectively transmit fuel without compromising system integrity. Always refer to the manufacturer's specifications and consider the dynamic pressure requirements to make an informed decision and maintain a reliable fuel system.
Outboard Motor Fuel Line: DIY Replacement Guide
You may want to see also
Frequently asked questions
Yes, it is possible to use a fuel hose as a temporary or even a permanent replacement for an air line, especially in situations where an air line is not readily available or if you are working with a limited budget. Fuel hoses are designed to handle fuel and can be a suitable alternative for air lines in certain applications.
Fuel hoses offer some benefits over air lines. They are often more flexible and can be easier to route through tight spaces. Additionally, fuel hoses are typically more durable and can withstand higher pressure, making them suitable for applications requiring robust performance.
While fuel hoses can be a viable option, there are a few considerations. Fuel hoses may not be as lightweight and flexible as dedicated air lines, which could impact their ease of use in certain installations. Additionally, if the fuel hose is not compatible with the specific fuel type, it may lead to performance issues or even safety hazards.
To ensure compatibility and safety, it is crucial to consult the manufacturer's guidelines and specifications for both the fuel hose and the air line system. Check the hose's pressure rating, temperature tolerance, and compatibility with the air line's internal components. Properly securing the hose and using appropriate fittings can also help prevent leaks and ensure a safe and efficient setup.