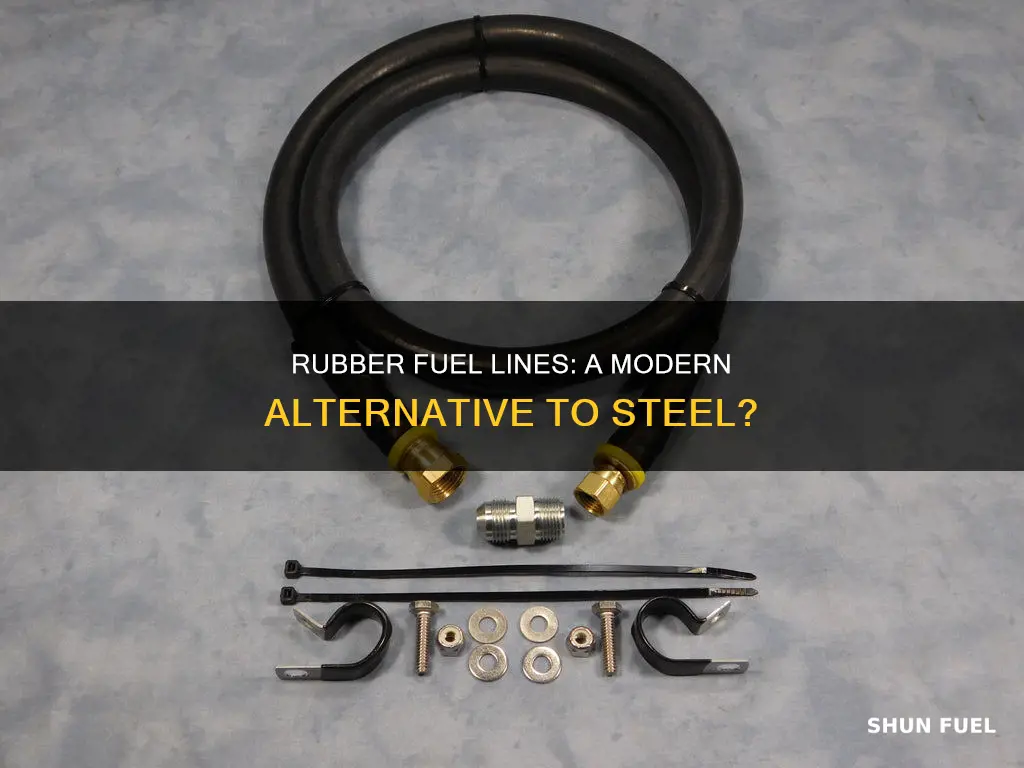
The debate over whether rubber fuel lines can replace steel in automotive applications has sparked interest among enthusiasts and engineers alike. While steel has long been the standard for fuel lines due to its durability and resistance to corrosion, rubber offers advantages such as flexibility and reduced weight. This comparison explores the potential benefits and drawbacks of using rubber fuel lines, considering factors like performance, longevity, and cost to determine if they can effectively replace steel in critical vehicle systems.
Characteristics | Values |
---|---|
Durability | Rubber fuel lines are generally less durable than steel and can be more susceptible to damage from heat, cold, and UV radiation. |
Flexibility | Rubber offers superior flexibility, allowing for easier installation and accommodating engine movement. |
Weight | Lighter than steel, reducing overall vehicle weight. |
Cost | Typically more affordable than steel fuel lines. |
Corrosion Resistance | Less resistant to corrosion compared to steel, especially in harsh environments. |
Temperature Tolerance | May have limitations in extreme temperatures, requiring careful selection. |
Installation | Easier to install due to flexibility, but may require specialized tools for some applications. |
Maintenance | Less maintenance required, but regular inspections are still necessary. |
Compatibility | May not be compatible with all fuel types and engine designs. |
Longevity | Generally shorter lifespan than steel, but can be extended with proper care. |
Environmental Impact | More environmentally friendly due to recyclability and reduced weight. |
What You'll Learn
Material Comparison: Rubber vs. Steel in Fuel Lines
The debate between rubber and steel as materials for fuel lines is an important consideration in the automotive and industrial sectors. Both materials have unique properties that make them suitable for different applications, and understanding their advantages and disadvantages is crucial for making informed decisions.
Rubber, a flexible and lightweight material, has been a popular choice for fuel lines due to its inherent flexibility. This flexibility allows rubber fuel lines to conform to the contours of the engine bay, providing a more compact and aesthetically pleasing installation. Additionally, rubber is known for its resilience, able to withstand minor impacts and vibrations without permanent deformation. This makes it an excellent choice for fuel lines, as it can absorb the shocks and vibrations that occur during vehicle operation. However, one of the main drawbacks of rubber is its susceptibility to degradation over time. Rubber fuel lines can crack, become brittle, or even leak due to exposure to fuel, heat, and UV radiation. This issue is particularly prevalent in older vehicles or those with high-performance engines, where the fuel lines are subjected to more extreme conditions.
On the other hand, steel offers superior strength and durability compared to rubber. Steel fuel lines are known for their ability to withstand high pressure and temperature, making them ideal for high-performance vehicles or those with larger fuel systems. The rigidity of steel ensures that the fuel lines maintain their shape and do not collapse under pressure, providing a more reliable and consistent fuel supply. Moreover, steel is highly resistant to corrosion, which is essential for long-term reliability. It can withstand the harsh environment of the engine bay, including exposure to fuel, oil, and other chemicals, without compromising its structural integrity. While steel fuel lines are more rigid and less flexible than rubber, this can be an advantage in certain applications, such as in high-vibration environments where flexibility is not a primary concern.
In terms of installation, rubber fuel lines often require more careful handling due to their flexibility. They can be more prone to kinking or bending out of shape if not installed correctly. Steel, being stiffer, is generally easier to work with and can be more forgiving during the installation process. However, the increased rigidity of steel may require more intricate routing to accommodate the engine's layout.
In conclusion, the choice between rubber and steel fuel lines depends on the specific requirements of the application. Rubber excels in flexibility and impact resistance, making it ideal for standard vehicles, while steel provides superior strength and durability, catering to high-performance or industrial needs. Understanding the unique properties of each material allows engineers and enthusiasts to make informed decisions, ensuring optimal fuel delivery and system longevity.
Replacing the Fuel Pump in a 98 Suburban: Step-by-Step Guide
You may want to see also
Durability: Rubber's Flexibility vs. Steel's Rigidity
The debate between rubber and steel fuel lines often centers on their respective strengths and weaknesses. Rubber fuel lines offer flexibility, which is advantageous in accommodating engine movement and vibrations. This flexibility can help prevent cracks and leaks that might occur in rigid steel lines due to the constant expansion and contraction of the engine. However, this very flexibility can be a double-edged sword. Rubber is more susceptible to damage from harsh chemicals, such as those found in fuel, and can degrade over time, especially in high-temperature environments. This degradation can lead to cracks and leaks, compromising the fuel system's integrity.
On the other hand, steel fuel lines are known for their rigidity and strength. They are less prone to the effects of fuel chemicals and can withstand high temperatures without significant degradation. This makes steel lines a reliable choice for high-performance engines or vehicles operating in extreme conditions. However, the rigidity of steel lines can be a disadvantage in certain applications. The lack of flexibility can lead to increased stress on the fuel lines, potentially causing cracks or even breaking if the engine moves excessively.
The choice between rubber and steel fuel lines ultimately depends on the specific requirements of the vehicle and its intended use. For everyday vehicles with standard operating conditions, rubber fuel lines might be sufficient and cost-effective. However, for high-performance or specialty vehicles, steel lines could be the better choice to ensure longevity and reliability. It's also worth noting that advancements in rubber technology have led to the development of synthetic rubbers that offer improved resistance to fuel chemicals and temperature changes, making them a more viable option for a wider range of applications.
In conclusion, while rubber fuel lines excel in flexibility, which is beneficial for engine movement, they may not be the best choice for all applications due to their susceptibility to fuel chemicals and temperature changes. Steel fuel lines, with their rigidity and strength, offer reliability and longevity but may not be as flexible as rubber. The decision should be based on a thorough understanding of the vehicle's needs and operating conditions.
Replacing the Fuel Filter in Your 2009 Hyundai Santa Fe
You may want to see also
Corrosion Resistance: Rubber's Vulnerability to Fuel
The debate over whether rubber fuel lines can replace steel in automotive applications often centers on one critical factor: corrosion resistance. Steel, a metal renowned for its strength and durability, has long been the go-to material for fuel lines due to its inherent resistance to corrosion from gasoline and diesel. However, rubber, while flexible and lightweight, is inherently more susceptible to corrosion when exposed to fuel.
Rubber's vulnerability to fuel is primarily due to its chemical composition. Natural and synthetic rubbers are organic materials that can degrade when exposed to hydrocarbons, such as those found in gasoline and diesel. This degradation process can lead to several issues:
- Cracking: Over time, the hydrocarbons in fuel can cause the rubber to crack and become brittle. These cracks can then allow fuel to seep into the surrounding areas, potentially causing further damage or creating a fire hazard.
- Swelling: Rubber can swell when exposed to fuel, leading to a loss of flexibility and potential failure of the fuel line. This swelling can also cause the fuel line to become less efficient, reducing the overall performance of the vehicle.
- Oxidation: While less common, some types of rubber can undergo oxidation when exposed to fuel, leading to a breakdown of the material's molecular structure. This process can result in a loss of elasticity and strength, further compromising the fuel line's integrity.
To mitigate these issues, engineers have developed specialized rubber compounds that are more resistant to fuel corrosion. These compounds often include additives that enhance the rubber's ability to resist swelling and cracking. However, even with these advancements, rubber fuel lines generally have a shorter lifespan compared to steel lines, especially in high-temperature environments or when exposed to certain types of fuels.
In conclusion, while rubber fuel lines offer advantages in terms of weight and flexibility, their susceptibility to corrosion from fuel is a significant consideration. Proper material selection and maintenance are crucial to ensuring the longevity and safety of fuel lines, whether they are made of rubber or steel.
Replacing Fuel Lines in a '96 Jeep Cherokee: DIY Guide
You may want to see also
Temperature Tolerance: Rubber's Limits in Extreme Conditions
The ability of rubber to withstand extreme temperatures is a critical factor when considering its use as a replacement for steel in fuel lines. Rubber has inherent limitations in terms of temperature tolerance, which can impact its performance and longevity in certain environments. Understanding these limits is essential for engineers and designers to make informed decisions when specifying materials for fuel line applications.
In general, rubber's temperature tolerance varies depending on its type and composition. Natural rubber, for instance, has a relatively low glass transition temperature (Tg), which is the point at which the material transitions from a hard, glassy state to a soft, rubbery state. This Tg is typically around 30-40°C (86-104°F). Below this temperature, natural rubber becomes brittle and can crack or break, while above it, the material becomes more flexible and elastic. This makes natural rubber unsuitable for applications requiring temperature resistance beyond this range.
On the other hand, synthetic rubbers, such as neoprene and silicone, offer improved temperature tolerance. Neoprene, for example, has a higher Tg of around 60-70°C (140-158°F), allowing it to maintain flexibility and resilience over a wider temperature range. Silicone rubbers, known for their excellent thermal stability, can withstand temperatures up to 300°C (572°F) without significant degradation. These synthetic rubbers are often preferred for fuel line applications due to their ability to operate in extreme conditions.
However, even with these advancements, there are still limitations. Rubber's temperature tolerance is not infinite, and prolonged exposure to extreme temperatures can lead to material degradation. High temperatures can cause rubber to become brittle, crack, or even melt, while low temperatures can make it stiff and less flexible. This is why it's crucial to select the appropriate rubber type and ensure it meets the specific temperature requirements of the application.
In summary, while rubber offers advantages over steel in terms of flexibility and cost-effectiveness, its temperature tolerance must be carefully considered. Engineers should choose rubber materials with suitable Tgs and ensure they are used within the recommended temperature range to avoid performance issues and ensure the longevity of the fuel lines. Understanding these limitations is key to making the right material choices in various industrial and automotive applications.
Replacing the Fuel Pump in Your 1996 Infiniti G20: Step-by-Step Guide
You may want to see also
Cost-Effectiveness: Rubber's Advantage Over Steel in Fuel Lines
The debate over whether rubber fuel lines can replace steel in automotive applications has been a topic of interest for many years, especially in the context of cost-effectiveness. While steel has traditionally been the go-to material for fuel lines due to its durability and strength, rubber has emerged as a compelling alternative, offering unique advantages that can significantly impact the overall cost of a vehicle's fuel system.
One of the primary reasons rubber fuel lines are cost-effective is their lightweight nature. Rubber is significantly lighter than steel, which translates to reduced material costs and improved fuel efficiency. Lighter fuel lines mean less strain on the engine, allowing for better performance and potentially longer engine life. This is particularly advantageous for high-performance vehicles or those with limited engine space, where every ounce of weight matters.
Additionally, rubber fuel lines are more flexible than steel, providing several benefits. Flexibility allows for easier installation, especially in tight spaces, reducing labor costs and potential damage during the installation process. Rubber's flexibility also contributes to better vibration dampening, which can lead to a smoother ride and reduced noise from the fuel system. This is a crucial factor in ensuring a comfortable driving experience and can be a selling point for vehicle manufacturers.
The cost-effectiveness of rubber fuel lines becomes even more apparent when considering the long-term savings. Rubber is generally more resistant to corrosion and degradation compared to steel, especially in harsh environmental conditions. This means that rubber fuel lines may have a longer lifespan, reducing the frequency of replacements and associated costs. Over time, the initial investment in rubber fuel lines can be offset by the reduced maintenance and repair expenses.
Furthermore, the manufacturing process of rubber fuel lines is often more efficient and environmentally friendly. Rubber can be produced in bulk, allowing for economies of scale, and its production requires less energy compared to steel manufacturing. This not only reduces the environmental impact but also contributes to lower production costs, making rubber fuel lines an attractive option for both manufacturers and consumers.
In conclusion, rubber fuel lines offer a compelling cost-effectiveness advantage over steel. Their lightweight design, flexibility, and long-term durability provide significant benefits in terms of fuel efficiency, installation ease, and reduced maintenance. As the automotive industry continues to prioritize cost-saving measures without compromising performance, rubber fuel lines present a viable and sustainable solution, ensuring a more affordable and efficient fuel system for vehicles.
Replacing Fuel Pump in Nissan Frontier: Step-by-Step Guide
You may want to see also
Frequently asked questions
Yes, rubber fuel lines can be a suitable alternative to steel lines in many applications. Rubber is flexible and can accommodate slight movements, making it ideal for fuel lines that need to bend or flex. It is also lightweight, easy to install, and offers good resistance to fuel leaks.
Rubber fuel lines have several benefits. They are more cost-effective than steel and are less prone to corrosion, which can be a common issue with steel lines over time. Rubber is also a better insulator, reducing the risk of fuel contamination from electromagnetic interference.
While rubber is durable, it may not be as strong as steel in terms of pressure resistance. Rubber can become brittle over time, especially in low-temperature environments, which could lead to cracks and potential fuel leaks. Proper installation and regular inspections are crucial to ensure the longevity of rubber fuel lines.
Yes, rubber fuel lines can be used in high-performance applications, but it requires careful consideration. The rubber should be of high quality and designed for the specific fuel type and temperature ranges expected in such vehicles. Regular maintenance and monitoring are essential to identify any signs of degradation.
It is recommended to consult your vehicle's manual or seek professional advice. Different vehicles have specific requirements, and factors like fuel type, engine design, and operating conditions play a role in determining the suitability of rubber fuel lines. Testing and compatibility checks may be necessary to ensure a safe and effective replacement.