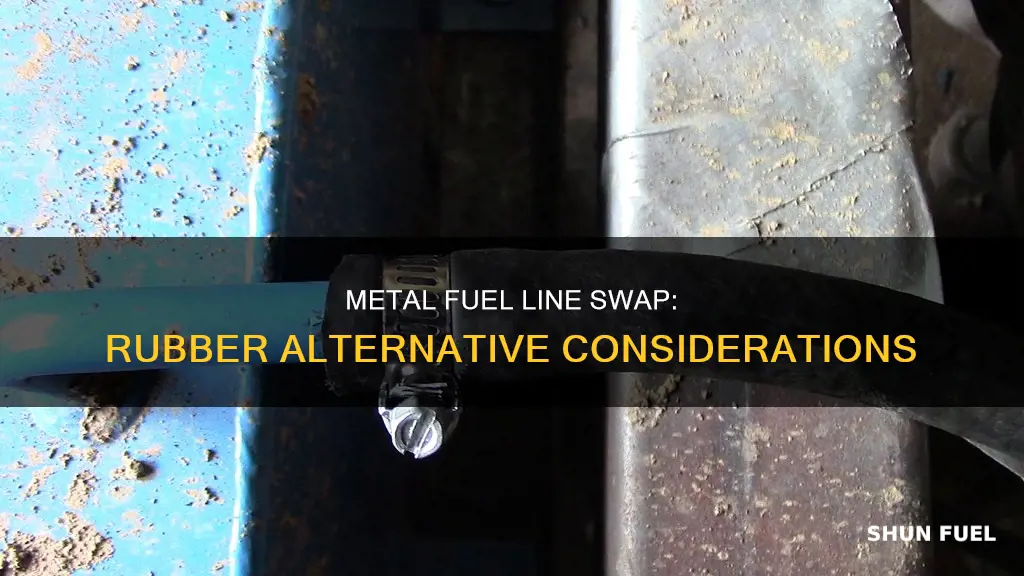
When considering the replacement of a metal fuel line with a rubber alternative, it's important to understand the implications of such a change. Metal fuel lines are known for their durability and resistance to corrosion, making them a reliable choice for transporting fuel in vehicles. However, rubber fuel lines offer flexibility and can be more cost-effective. This raises the question: Can a metal fuel line be safely and effectively replaced with a rubber one? The answer depends on various factors, including the specific application, environmental conditions, and the quality of the rubber material used. This introduction sets the stage for a detailed exploration of the feasibility and considerations involved in making such a replacement.
Characteristics | Values |
---|---|
Durability | Rubber fuel lines are generally more flexible and less prone to cracking compared to metal, making them suitable for high-vibration environments. |
Temperature Resistance | Rubber can withstand a wide range of temperatures, making it a good choice for fuel lines that may experience extreme temperature fluctuations. |
Corrosion Resistance | Metal fuel lines are more susceptible to corrosion, especially in the presence of fuel contaminants. Rubber lines are less prone to corrosion and can provide better long-term performance. |
Flexibility | Rubber offers superior flexibility, allowing for easier installation and accommodating engine movement without permanent deformation. |
Cost | Rubber fuel lines are often more affordable than metal alternatives, making them a cost-effective option for replacements. |
Maintenance | Rubber lines typically require less maintenance and are less likely to require frequent replacements due to wear and tear. |
Compatibility | Rubber can be compatible with various fuel types, including gasoline, diesel, and ethanol blends, making it a versatile choice. |
Installation | Installation of rubber fuel lines is generally simpler and quicker, reducing labor costs and installation time. |
Weight | Rubber is lighter than metal, which can be advantageous in certain vehicle applications where weight reduction is a priority. |
Longevity | With proper care and maintenance, rubber fuel lines can have a long service life, often outperforming metal lines in harsh conditions. |
What You'll Learn
- Safety Considerations: Metal fuel lines are safer than rubber due to their durability and resistance to punctures
- Performance Impact: Rubber fuel lines may affect engine performance due to their flexibility and potential for leaks
- Legal Regulations: Check local laws regarding the use of rubber fuel lines in vehicles
- Cost Analysis: Compare the costs of metal and rubber fuel lines to make an informed decision
- Installation Process: Proper installation techniques are crucial for both metal and rubber fuel lines
Safety Considerations: Metal fuel lines are safer than rubber due to their durability and resistance to punctures
When it comes to fuel lines, safety is paramount, especially in vehicles where the integrity of the fuel system is crucial for operation and, more importantly, for the driver's and passengers' safety. One of the primary considerations in this context is the material used for the fuel lines. Traditionally, metal fuel lines have been the preferred choice due to their inherent safety advantages over rubber.
Metal fuel lines offer superior durability and resistance to punctures, which are critical factors in ensuring the safe operation of a vehicle. Rubber, while flexible and easy to install, is inherently more susceptible to damage from sharp objects, road debris, and even temperature fluctuations. Over time, rubber fuel lines can crack, split, or even rupture, leading to potential fuel leaks, which pose significant safety risks. Metal, on the other hand, is much stronger and less prone to degradation under various environmental conditions.
The resistance of metal fuel lines to punctures is a key safety feature. Metal lines are less likely to be pierced by sharp objects that might be encountered on the road, such as nails, glass, or even the sharp edges of other vehicles during a collision. This resistance to puncture is vital in preventing fuel leaks, which can lead to fires or explosions, especially in the event of a crash. Metal's strength and rigidity provide a robust barrier that safeguards the fuel system from potential hazards.
Furthermore, the durability of metal fuel lines is an essential safety consideration. Metal lines can withstand the rigors of the road environment, including exposure to sunlight, heat, and cold. They are less likely to become brittle or crack over time, ensuring that the fuel system remains intact and functional for the long term. This durability is particularly important in high-performance vehicles or those used in extreme conditions, where the fuel system must be reliable and safe under all circumstances.
In summary, metal fuel lines offer a higher level of safety compared to rubber due to their superior durability and resistance to punctures. These properties are essential in maintaining the integrity of the fuel system, preventing leaks, and ensuring the overall safety of the vehicle and its occupants. While the initial cost of metal fuel lines might be higher, the long-term benefits in terms of safety and reliability make them a wise investment for any vehicle owner.
Subaru Forester Fuel Door Replacement: A Step-by-Step Guide
You may want to see also
Performance Impact: Rubber fuel lines may affect engine performance due to their flexibility and potential for leaks
The decision to replace metal fuel lines with rubber alternatives can have a significant performance impact on an engine, primarily due to the inherent properties of rubber. Rubber fuel lines are known for their flexibility, which can be both a benefit and a potential drawback. On one hand, this flexibility allows the lines to absorb vibrations and shocks from the engine, reducing the risk of damage and improving overall engine longevity. This is especially beneficial in high-performance applications where engines operate under extreme conditions. However, this flexibility also introduces a unique set of challenges.
One of the primary concerns with rubber fuel lines is their potential for leaks. Over time, the rubber material can degrade, becoming more susceptible to cracks and punctures. This degradation is often accelerated by factors such as temperature fluctuations, fuel type, and the presence of contaminants in the fuel. Leaks in the fuel lines can lead to a loss of power, reduced engine performance, and even potential engine damage. The flexibility of rubber lines can also make it easier for air to enter the fuel system, causing air bubbles that can further contribute to performance issues.
The performance impact of rubber fuel lines is often more noticeable in high-performance engines where precise fuel delivery is critical. In such applications, the flexibility of rubber lines can lead to inconsistent fuel flow, affecting the engine's ability to maintain optimal performance, especially during rapid acceleration or high-load conditions. Additionally, the potential for leaks becomes a more significant issue, as even a small leak can result in a noticeable drop in power and efficiency.
To mitigate these performance impacts, regular maintenance and inspection of rubber fuel lines are essential. This includes checking for any signs of wear, cracks, or leaks, and replacing the lines if necessary. Upgrading to high-quality, reinforced rubber fuel lines can also help improve performance and longevity. In some cases, a combination of rubber and metal fuel lines may be used, with rubber lines employed in areas where flexibility is beneficial and metal lines used for critical components that require rigidity.
In summary, while rubber fuel lines offer advantages in terms of flexibility and vibration absorption, they also introduce performance considerations. The potential for leaks and the impact on fuel delivery can significantly affect engine performance, especially in high-performance applications. Understanding these factors is crucial for engine enthusiasts and mechanics when deciding on fuel line replacements to ensure optimal engine operation.
Replacing the Fuel Pump in Your 2008 Infiniti G35x Sedan
You may want to see also
Legal Regulations: Check local laws regarding the use of rubber fuel lines in vehicles
When considering the replacement of metal fuel lines with rubber in vehicles, it is crucial to be aware of the legal regulations and standards that may apply in your region. The use of rubber fuel lines is not universally permitted, and local laws can vary significantly. Here's a guide on what you need to know:
Research Local Vehicle Modification Regulations: Start by researching the specific laws and regulations governing vehicle modifications in your area. Many regions have strict rules regarding the alteration of vehicle components, including fuel lines. These regulations are often designed to ensure vehicle safety, environmental protection, and compliance with industry standards. Check with your local department of motor vehicles (DMV) or relevant authorities to understand the specific requirements.
Check for Vehicle Manufacturer Guidelines: Before making any modifications, it is essential to consult the vehicle manufacturer's guidelines. Some manufacturers provide detailed instructions and recommendations for fuel line replacements. They may specify approved materials and methods to ensure the vehicle's performance, safety, and warranty coverage. Adhering to these guidelines is crucial to avoid any legal issues or voiding your vehicle's warranty.
Understand the Purpose of Fuel Lines: Metal fuel lines are typically used for their durability and ability to withstand high pressure. Rubber fuel lines, while flexible, may not provide the same level of structural integrity. Local regulations might be in place to ensure that fuel lines can withstand the stresses of the vehicle's operation. Check if there are specific requirements regarding the material, thickness, and construction of fuel lines to ensure compliance with safety standards.
Environmental and Safety Considerations: Rubber fuel lines might raise concerns regarding environmental impact and safety. Some regions have regulations to prevent the use of materials that could potentially leak harmful substances into the environment. Additionally, the flexibility of rubber fuel lines may require specific safety measures to prevent damage during vehicle operation. It is essential to understand these considerations to ensure your modifications comply with local laws.
Consult Legal Professionals: If you are unsure about the legal implications, consider consulting legal professionals or automotive experts who are familiar with local regulations. They can provide guidance tailored to your region, helping you navigate the legal requirements and ensuring your modifications are in compliance with all applicable laws.
Replacing Fuel Pump Wires: A Step-by-Step Guide
You may want to see also
Cost Analysis: Compare the costs of metal and rubber fuel lines to make an informed decision
When considering the replacement of a metal fuel line with a rubber alternative, a cost analysis is essential to make an informed decision. The initial cost of a metal fuel line is generally higher compared to its rubber counterpart. Metal lines, often made of steel or aluminum, offer durability and longevity, making them a preferred choice for many vehicle owners. However, the upfront investment can be a significant factor for some. On the other hand, rubber fuel lines are typically more affordable, providing a cost-effective solution for those seeking a replacement. This initial price difference can be a deciding factor for many, especially those on a tight budget.
The long-term costs associated with each material should also be considered. Metal fuel lines, while expensive upfront, often have a longer lifespan, reducing the need for frequent replacements. This can result in significant savings over time, as the cost of multiple replacements with rubber lines could accumulate. Rubber, being more flexible and less rigid, may require more frequent replacements due to potential wear and tear, especially in high-pressure environments. This increased maintenance cost should be factored into the overall decision-making process.
Another aspect to consider is the complexity of the installation process. Metal fuel lines often require specialized tools and a higher level of skill, which can add to the overall cost. The installation of rubber lines, while generally simpler, may still incur additional expenses if professional assistance is needed. It is important to weigh these installation costs against the potential savings or benefits of choosing one material over the other.
Additionally, the availability and ease of sourcing these materials play a role in the cost analysis. Metal fuel lines, being more common and widely used, are usually more readily available, which can influence the overall price. Rubber lines, while becoming more popular, might have limited options, especially for custom-fit applications, potentially increasing costs.
In conclusion, the decision to replace a metal fuel line with rubber should be based on a comprehensive cost analysis. While metal lines offer durability and potentially lower long-term costs, rubber lines provide an initial budget-friendly solution. The installation process, availability, and potential maintenance requirements should also be considered to make an informed choice that aligns with the user's financial goals and preferences.
Replacing Your Boat's Fuel Tank: A Step-by-Step Guide
You may want to see also
Installation Process: Proper installation techniques are crucial for both metal and rubber fuel lines
The process of replacing a metal fuel line with a rubber alternative requires careful attention to detail and specific techniques to ensure a secure and reliable connection. While rubber fuel lines offer flexibility and can be more resistant to vibration, the installation process is distinct from that of metal lines. Here's an overview of the steps involved:
Preparation: Begin by gathering the necessary tools and materials, including the new rubber fuel line, fittings, and any required adhesives or sealants. Ensure that the old metal line has been removed or securely disconnected to create a clean slate for the new installation. Inspect the fuel system for any signs of damage or corrosion that might affect the integrity of the connection.
Measuring and Cutting: Accurate measurements are essential. Measure the length of the rubber fuel line required, ensuring it matches the original metal line's length. Cut the rubber line carefully using a sharp blade or a dedicated fuel line cutter. The cut should be clean and precise to avoid any rough edges that could compromise the seal.
Fitting Installation: Install the fittings onto the ends of the rubber fuel line. Ensure a snug fit by using the appropriate tools to press the fittings onto the line. Follow the manufacturer's guidelines for the specific torque values and installation procedures for the fittings. Properly aligned and tightened fittings are crucial to prevent leaks and ensure a secure connection.
Assembly and Connection: With the fittings in place, assemble the fuel line into the system. Slide the fittings onto the corresponding fuel line ports, ensuring they are aligned correctly. Use fuel line connectors or clamps to secure the fittings and the line in place. Double-check that all connections are tight and free from any gaps or misalignments.
Testing and Inspection: After the installation, it is vital to test the system for any leaks. Apply a small amount of fuel or a suitable sealant to the connections and observe for any signs of leakage. If no leaks are detected, further testing can be conducted by applying pressure to the system and checking for any drips. Inspect the entire installation, including the fittings and connections, to ensure everything is secure and intact.
Remember, proper installation techniques are critical to the performance and safety of the fuel system. Rubber fuel lines may offer advantages in flexibility, but they still require careful handling and installation to ensure optimal functionality and longevity. Always refer to the manufacturer's instructions and guidelines for the specific products being used to guarantee a successful and safe replacement.
Replacing Stihl Trimmer Fuel Filter: Step-by-Step Guide
You may want to see also
Frequently asked questions
While it is possible to replace a metal fuel line with a rubber one, it is generally not recommended for several reasons. Rubber fuel lines are more susceptible to cracking, especially in environments with extreme temperatures or exposure to sunlight. This can lead to fuel leaks, which pose a significant safety hazard.
Metal fuel lines, typically made of steel or aluminum, offer several advantages. They are highly durable and can withstand high pressure and temperature changes. Metal lines are less flexible but more resistant to kinking and are less likely to develop leaks over time.
Rubber fuel lines are generally not suitable for high-performance or racing applications. The flexibility of rubber can lead to increased fuel pressure drop and potential performance issues. In high-performance vehicles, metal fuel lines are preferred for their rigidity and ability to maintain consistent fuel pressure.
There are several signs that may indicate your fuel line needs replacement. These include fuel leaks, engine misfires, reduced engine performance, or the presence of fuel odor in the cabin. Regular maintenance and inspections can help identify potential issues before they become major problems.
Replacing a fuel line requires specialized tools and techniques to ensure a proper and safe installation. It is recommended to have the necessary experience or seek professional assistance to avoid potential hazards. Proper sealing, crimping, and torque specifications must be followed to ensure a reliable connection.