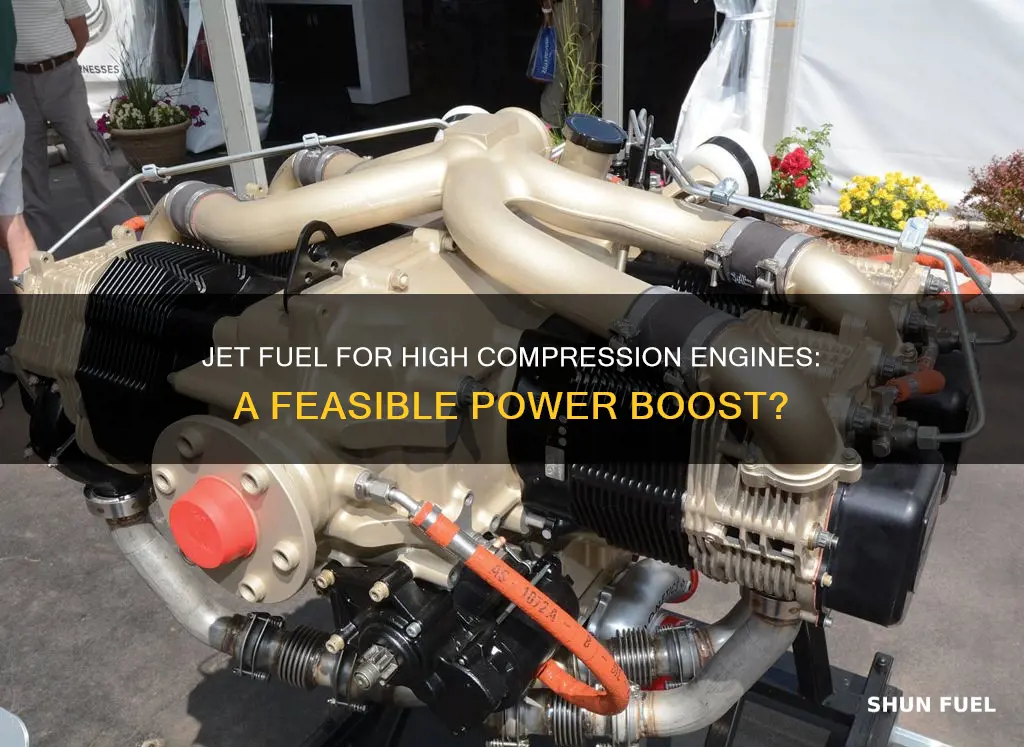
Can a high compression car engine run on jet fuel? This question delves into the compatibility of jet fuel with high compression engines, a topic of interest for those exploring alternative fuels and engine modifications. Jet fuel, known for its high energy density, presents an intriguing possibility for enhancing engine performance. However, the compatibility of jet fuel with high compression engines, which are designed to operate on conventional gasoline or diesel, requires careful consideration. This exploration aims to shed light on the feasibility and potential benefits of using jet fuel in high compression car engines, offering insights into the intersection of fuel choice and engine design.
Characteristics | Values |
---|---|
Engine Type | High Compression |
Fuel Compatibility | Jet Fuel (Avgas) |
Performance Impact | Improved power and efficiency |
Engine Modifications | Required (e.g., piston rings, valves) |
Fuel Efficiency | Potentially higher due to denser fuel |
Octane Requirement | High octane jet fuel |
Engine Reliability | Potential risks with improper fuel use |
Emission Levels | Potentially lower due to denser fuel |
Cost Implications | Higher initial setup costs |
Legal Considerations | Jet fuel availability and regulations |
Environmental Impact | Lower carbon emissions compared to gasoline |
Engine Lifespan | Potential for longer engine life with proper maintenance |
Safety Measures | Required precautions for handling and storage |
What You'll Learn
- Engine Design: High compression engines may require specific jet fuel adaptations for optimal performance
- Fuel Injection: Jet fuel's properties can impact fuel injection systems and engine management
- Combustion Chamber: Jet fuel's combustion characteristics differ, affecting engine compression and power output
- Engine Materials: Jet fuel's corrosive nature may require specialized materials to withstand high compression
- Performance Testing: Real-world testing is crucial to assess engine performance with jet fuel under high compression
Engine Design: High compression engines may require specific jet fuel adaptations for optimal performance
High compression engines, known for their ability to produce high power outputs, often require careful consideration when it comes to fuel choice and engine design. While jet fuel is a high-octane aviation fuel, it is not typically the first choice for automotive applications due to its unique properties and the specific requirements of high compression engines. However, with the right adaptations, it is indeed possible to utilize jet fuel in these engines, offering a unique performance advantage.
The key to making this work lies in the engine's design and the fuel's properties. Jet fuel has a higher energy density and a different chemical composition compared to conventional gasoline or diesel. It contains a higher percentage of aromatic hydrocarbons, which provide excellent lubricity but can also lead to increased engine wear if not properly managed. High compression engines, with their tightly packed pistons and rapid combustion, benefit from the high energy content of jet fuel, which can result in improved power output and efficiency.
Engine designers must consider several factors to ensure optimal performance. Firstly, the fuel injection system needs to be precisely calibrated to deliver the correct amount of jet fuel at the right pressure and temperature. This is crucial as jet fuel's volatility and combustion characteristics differ from those of conventional fuels. Secondly, the engine's compression ratio should be carefully matched to the fuel's octane rating. High compression engines often require fuels with higher octane levels to prevent engine knock, which can lead to reduced performance and potential damage.
Additionally, the use of jet fuel may necessitate modifications to the engine's cooling system. Jet fuel's higher heat content can result in increased engine temperatures, requiring more efficient cooling mechanisms to maintain optimal operating conditions. Furthermore, the engine's lubrication system should be designed to handle the unique properties of jet fuel, ensuring adequate protection against wear and tear.
In summary, while high compression engines can technically run on jet fuel, specific adaptations are required in engine design and fuel management. These adaptations ensure that the engine's performance is optimized, and the unique properties of jet fuel are harnessed effectively. With the right adjustments, high compression engines can offer a powerful and efficient driving experience, showcasing the versatility of engine technology.
Bad Fuel Injector: Why Your Car Won't Start
You may want to see also
Fuel Injection: Jet fuel's properties can impact fuel injection systems and engine management
Jet fuel, a high-octane aviation fuel, is an intriguing option for powering high-compression car engines. While it may seem counterintuitive, the properties of jet fuel can indeed be harnessed to optimize performance in these engines. The key lies in understanding the unique characteristics of jet fuel and how they interact with fuel injection systems and engine management.
One of the primary advantages of jet fuel is its high energy density. This property allows for more efficient combustion, resulting in increased power output and improved engine performance. However, this also means that the fuel must be carefully managed to prevent excessive pressure and potential damage to the engine. Fuel injection systems play a critical role in this process. These systems precisely control the amount of fuel injected into the engine, ensuring optimal combustion while minimizing waste. When using jet fuel, the injection system must be finely tuned to account for its higher energy content. This involves adjusting the fuel-air mixture, spray patterns, and injection timing to maintain the desired combustion efficiency without overloading the engine.
The volatility of jet fuel is another crucial factor. Jet fuels are designed to vaporize quickly at high temperatures, which can be beneficial for starting the engine in cold conditions. However, this volatility also requires careful management to prevent fuel atomization issues. The fuel injection system must ensure that the jet fuel is atomized into fine droplets, allowing for efficient mixing with air and combustion. This may involve using specialized nozzles or injectors that can handle the unique flow characteristics of jet fuel.
Engine management systems are essential for optimizing performance and ensuring safe operation. These systems monitor various engine parameters, such as temperature, pressure, and combustion efficiency. When using jet fuel, the engine management system must be programmed to account for its different combustion characteristics. This includes adjusting the air-fuel ratio, ignition timing, and other parameters to maintain optimal performance while ensuring the engine operates within safe limits. Proper engine management is crucial to prevent issues like pre-ignition, knock, or excessive engine wear.
In summary, while jet fuel may not be a conventional choice for high-compression car engines, its unique properties can be harnessed to enhance performance. The fuel injection system and engine management play critical roles in optimizing combustion, atomization, and overall engine operation. By understanding and carefully managing the characteristics of jet fuel, engineers can create efficient and powerful engine systems that leverage the benefits of this high-energy fuel.
Are Fuel Cell Cars the Greenest Option? Unveiling the Truth
You may want to see also
Combustion Chamber: Jet fuel's combustion characteristics differ, affecting engine compression and power output
The combustion chamber of an engine is a critical component that plays a pivotal role in the efficient burning of fuel, and this becomes even more crucial when considering the use of jet fuel in high-compression car engines. Jet fuels, derived from petroleum, possess unique combustion characteristics that set them apart from conventional gasoline or diesel. These differences can significantly impact the engine's performance, particularly in terms of compression and power output.
One key aspect is the volatility of jet fuels. These fuels are designed to vaporize quickly at high temperatures, which is essential for efficient combustion. When a high-compression car engine operates with jet fuel, the rapid vaporization ensures that the fuel-air mixture is atomized effectively, allowing for a more complete and rapid combustion process. This results in improved power output and a more responsive engine. However, this volatility also means that the engine's compression ratio must be carefully calibrated to manage the rapid fuel vaporization without causing issues like pre-ignition or engine knock.
The combustion characteristics of jet fuels also influence the engine's ability to maintain a consistent burn rate. Jet fuels typically have a higher cetane number compared to gasoline, which means they ignite more readily under compression. This can lead to a more controlled and efficient combustion process, especially in high-compression engines. As a result, the engine can extract more energy from the fuel, potentially increasing power output and overall engine performance.
Additionally, the combustion chamber design becomes even more critical when using jet fuel. The chamber's geometry and volume can be optimized to accommodate the unique combustion characteristics of jet fuels. Engineers might adjust the chamber's size and shape to ensure proper fuel-air mixing and efficient combustion. This optimization process is essential to harness the full potential of jet fuel in high-compression engines without compromising performance or efficiency.
In summary, the combustion chamber's role in managing the unique combustion characteristics of jet fuels is vital for the successful operation of high-compression car engines. By understanding and tailoring the chamber's design to the specific properties of jet fuels, engineers can maximize power output, improve engine response, and ensure efficient combustion, ultimately making it a feasible and attractive option for high-performance vehicle applications.
Fuel Filter Issues: Why Your Car Won't Start
You may want to see also
Engine Materials: Jet fuel's corrosive nature may require specialized materials to withstand high compression
The idea of using jet fuel in high-compression car engines is an intriguing concept, but it presents a unique challenge due to the corrosive nature of jet fuels. These fuels, primarily composed of kerosene, contain additives and impurities that can be highly detrimental to engine components over time. The high compression ratios found in modern car engines, often exceeding 10:1, create an environment where even small amounts of corrosive substances can lead to significant engine damage.
Engine materials play a critical role in ensuring the longevity and performance of the engine when running on jet fuel. Traditional engine materials, such as aluminum alloys and cast iron, may not be sufficient to withstand the corrosive effects of jet fuel. The fuel's acidic nature can lead to the degradation of these materials, causing issues like piston ring wear, cylinder head damage, and even engine failure.
To combat this, engineers and material scientists have developed specialized materials that can better resist the corrosive properties of jet fuel. One such material is a type of stainless steel alloy, specifically designed to handle the high temperatures and corrosive elements of jet fuel. This alloy contains a higher percentage of chromium, which forms a protective oxide layer on the surface, preventing the fuel from corroding the metal.
Additionally, the use of advanced coatings and surface treatments can further enhance the engine's durability. Plasma-sprayed ceramic coatings, for instance, can provide a protective barrier between the engine components and the jet fuel. These coatings are highly resistant to corrosion and can significantly extend the engine's lifespan when running on jet fuel.
In summary, the corrosive nature of jet fuel requires careful consideration of engine materials to ensure optimal performance and longevity. Specialized materials, such as advanced stainless steel alloys and protective coatings, are being developed to withstand the challenges posed by high-compression car engines running on jet fuel. These innovations are crucial in making the concept of jet-fueled high-performance cars a reality.
Fuel Cells vs. Gas: The Green Car Debate
You may want to see also
Performance Testing: Real-world testing is crucial to assess engine performance with jet fuel under high compression
Real-world performance testing is an essential step in evaluating the feasibility of using jet fuel in high-compression car engines. This testing phase provides critical insights into the engine's behavior and efficiency when operating with a different fuel type, especially one with unique properties like jet fuel. The primary objective is to ensure that the engine can deliver optimal performance while maintaining reliability and longevity when fueled with jet fuel.
Performance testing involves a series of rigorous experiments and simulations to mimic real-world conditions. Engineers and technicians subject the engine to various load and speed conditions, simulating different driving scenarios. This includes testing at high loads and speeds, which are typical during acceleration and high-speed cruising. By doing so, they can assess the engine's response and performance characteristics under these demanding conditions.
One critical aspect of performance testing is evaluating the engine's power output and efficiency. Jet fuel, with its higher energy content compared to conventional gasoline or diesel, can potentially offer improved power and efficiency. However, the high compression ratio of the engine must be considered, as it can significantly impact fuel atomization and combustion. Testing helps determine if the engine can harness the energy potential of jet fuel effectively while maintaining optimal combustion efficiency.
Additionally, performance testing includes analyzing the engine's emissions and exhaust characteristics. Jet fuel combustion may produce different byproducts and exhaust gases, and testing ensures that these emissions meet environmental standards and do not compromise the engine's performance. This is crucial, especially when considering the potential use of jet fuel in high-performance or racing applications.
The real-world testing process also involves monitoring the engine's durability and longevity. High-compression engines fueled with jet fuel may experience unique wear and tear patterns, and testing helps identify any potential issues. This includes assessing the engine's ability to handle the corrosive effects of jet fuel, especially in high-temperature and high-pressure environments. By conducting these tests, engineers can make informed decisions about the engine's suitability for jet fuel operation and any necessary modifications to ensure optimal performance and longevity.
Hydrogen Car Fuel Costs: A Comprehensive Guide to Pricing
You may want to see also
Frequently asked questions
Yes, it is possible to modify a high compression car engine to run on jet fuel. Jet fuel has a higher energy density compared to gasoline, which can provide more power and efficiency. However, the engine design and components need to be compatible with the fuel's properties, including its higher flash point and different combustion characteristics.
Jet fuel offers several benefits. Firstly, it has a higher octane rating, allowing for higher compression ratios and potentially increased power output. Secondly, jet fuel's lower sulfur content results in cleaner combustion, reducing emissions of harmful pollutants. Additionally, jet fuel can provide better fuel economy due to its higher energy content.
Modifying the fuel injection system is often necessary. Jet fuel requires precise fuel-air mixture management due to its different combustion properties. This may involve adjusting the fuel injectors, using a different fuel pump, and potentially recalibrating the engine's electronic control unit (ECU) to ensure optimal performance and efficiency.
Yes, a hybrid approach is possible. Some car enthusiasts use a blend of jet fuel and gasoline, often in a specific ratio, to take advantage of the benefits of both fuels. This can provide a balance between power, efficiency, and cost. However, careful consideration of the fuel mixture and engine calibration is essential to avoid potential issues.
While jet fuel can offer advantages, there are challenges. Jet fuel's higher cost and limited availability compared to gasoline may be a concern. Additionally, the engine's performance and longevity need to be closely monitored due to the different combustion characteristics of jet fuel, which can put additional stress on certain engine components. Proper maintenance and regular inspections are crucial.